Introduction As a material for boat building, fibreglass has gained in popularity over wood and metal in both developed and developing countries, mainly because of the relative simplicity of construction, the ability to produce many identical hulls from a single mould, and the ease of maintenance of the boats themselves. Fibreglass boats are completely watertight, rot-proof and resistant to borers.
Disadvantages of fibreglass stem from the health risks associated with inhalation of fibre dust during construction, and the fact that the boats are slow to degrade and disposal at fiberglass resin for boat building quality end of their life is difficult. Fibreglass is a term used to describe Fibre Reinforced Plastic FRPa material consisting of glass fibre impregnated with resin. Typically, a hardwearing surface is created with the use of a gel coat, strengthened by layers of fibreglass mat impregnated with resin.
The required strength is achieved either by using several layers of mat or by using a thicker gauge of mat. Materials and equipment The key to producing high quality boats is a good mould - a mirror image of the finished hull, which is also a fibreglass construction cast from either a plug, which is wooden replica of a hull, or the hull of an existing boat.
In Sri Lanka, it is almost always an existing hull that is used to create the mould. Once the mould is created, it can be used to build hundreds of boats, which will have precisely the same shape as the original boat or plug used to create the mould.
Therefore, it is very important that a good boat with the perfect hull shape is selected for this purpose. The better the plug, the better the mould and all the boats that come out of it. For larger vessels the plug and mould building is repeated for the deck and interior moulds.
Company Reg. Charity No. Glass fibre Glass is processed into filaments then woven or fiberglass resin for boat building quality and supplied in rolls of matting. The thickness of the cloth or mat varies with the weight of the fiberglass resin for boat building quality in grams per square metre.
Type E glass should be used for tropical marine use. Reinforcement materials are supplied in rolls sealed in polythene bags inside cardboard boxes. On delivery the material should be checked for contamination by dirt, oil or water. If spoiled, it is unusable. Fiberglass resin for boat building quality checking, the rolls, they should be re-sealed to prevent contamination by high humidity.
If damp, the bonding between the resin and mat are weakened. Chopped strand mat CSM The continuous filament is held together with a binder to form a continuous sheet of chopped strand mat of variable thickness. One side of the material is slightly smoother than the. It is the rougher side which should be placed down when laminating. WR has a high tensile strength and also gives a higher glass per unit volume ratio than CSM, which means less resin is needed, and therefore is cheaper to use.
Approximate resin to glass ratio for CSM is 2. WR is rarely used in vessels of less than 6 m. CSM laminates are normally adequate for smaller boats. It is used to support a thick gel coat or to produce a smooth finish on the innermost layer of a laminate. Core mat This is a course mat that is specified by thickness rather than weight.
Fiberglass resin for boat building quality is used only for specific areas which require extra strengthening. Resins All resins should be stored in a cool, shaded and ventilated place. The usual shelf life for resin is given as 6�12 months, but it can be used as long as it is liquid.
Pre-accelerated resins have a shorter shelf life than pure resin. Lay-up or laminating resins The laminating resin a translucent liquid of pale colour provides the medium within which the fibreglass mat is bedded. The resin is usually supplied in litre drums, but can fiberglass resin for boat building quality be bought in smaller quantities from retail suppliers.
Gel coat resin The gel coat resin is a more viscous liquid. When cured, the gel coat forms the shiny, smooth, weather resistant outer surface of the hull. Resin putty This material is used as filler, or for bedding deck fittings or filling internal corners on joints which require bonding. Since it is composed mostly of a filler powder, which is water absorbent, it should not be used on underwater surfaces unless based on an epoxy resin.
A coating of PVA is used to prevent the mould from sticking to the plug or finished hull. Catalysts and accelerators To cure hardenresin requires a catalyst and an accelerator. Resin can be ordered with or without the accelerator pre-mixed.
Pre-accelerated resin is recommended because the supplier is able to make a more thorough mix; and it is one less step for the user. When using un- accelerated resin, the accelerator should be thoroughly mixed in. Accelerator and catalyst must never be mixed directly together as this could cause an explosion.
Material Quantity kg Mirror Glaze Wax 0. Mixing resin or gel coat Resin is stored in drums in a cool, shaded place, preferably in a separate resin room. There should be a drip tray beneath the tap.
Between fiberglass resin for boat building quality tap and the tray will be enough room to place a 5�10 L plastic bucket, which can be filled with resin for use by a laminator. Every two days, the drum should be rotated by and the tap removed and cleaned with acetone, to prevent blockage. Outside the resin room should be a two separate store cupboards for catalyst and for accelerator.
Accelerator can be added during the preparation stage and mix well with a clean, disposable wooden stick. The amount of accelerator added will be determined based on the weather conditions humidity.
Catalyst is only added at the very last moment before laminating begins, when everything else is ready. Both these additives are supplied in 20 or 5 L plastic drums not in steel containers because resin reacts with rust and are fiberglass resin for boat building quality to refill 1 L plastic bottles fitted with a graduated pourer for final mixing.
In the case of gel coat, a colour pigment will have been added to uncoloured gel coat according to supplier's mixing ratios. Standard white pre-pigmented resin is widely available as it is the most popular hull and superstructure colour. Preparing the mat The task of storing and cutting the mat may be allocated to one labourer who then becomes skilled at this task. For preparation, a cutting table is needed see picture with a vertical rack for the rolls of different types of reinforcement from which appropriate lengths can be drawn and cut and then re-rolled and labelled fiberglass resin for boat building quality a felt tip pen to indicate to the laminators what it is.
It is good practise to use a plywood template for each section of mat needed. Lengths up to 10 m fiberglass resin for boat building quality be prepared on a shorter cutting table by folding the reinforcement.
The Credit: Practical Action South Asia table edge should have graduations at 10 cm intervals to fiberglass resin for boat building quality precise measurement.
A sharp knife is needed for cutting and since glass reinforcement blunts steel blades very quickly, they should be sharpened. A straight edge is needed to cut the glass to length. An aluminium strip is best as it is light to handle and does not contaminate the cloth.
For cutting curves, a felt tip pen or chalked line can be drawn for guidance and the cut made freehand whilst allowing a 10 cm margin. Industrial quality scissors may also be of use. Preparing the plug To begin, place the plug fiberglass resin for boat building quality existing hull being used to create to mould upside down on a level floor, and make sure the plug is absolutely level using a spirit level or transparent flexible tube filled with water.
At the deck edge, which is in this case near the floor, attach fiberglass resin for boat building quality plywood flange so that later during the moulding process, gelled Fibreglass can be trimmed back to leave a solid laminate with a clean cut edge. If the plug is wooden, cover the plug with a Fibreglass skin.
This layer can then be filled where necessary with resin putty to remove the shallow indentations, which will show up once the fibreglass skin is consolidated.
Remove any irregularities by grinding or by hand sanding. Repeat this process of hand finishing until the plug is smooth enough to receive a layer of hard tooling gel coat. This especially formulated gel coat is the beginning of the coating, which will eventually give the polished surface from which the mould will be lifted.
The plug and mould gel coat should be black in colour, to contrast with the finished hull. There is no shortcut at this stage. The more time that is spent hand sanding the plug with wet and dry sandpaper, the better the plug will be.
After applying the gel coat, further filling with resin putty and sanding may be necessary for a good finish. In some cases the gel coat layer on the plug is omitted and only cataloy paste is used to fill imperfections.
Finally, polish with rubbing paste and then with 5�7 coats of non-silicone wax to give a brilliant sheen, before applying a coat of PVA release agent, which is the last step before fiberglass resin for boat building quality mould itself is begun. Five workers would take at least a week for the final preparation of a plug for a 10 m hull.
Making the mould If the shape of the hull is such that the mould has acute release angles, a split mould, rather than a one-piece mould, is necessary. The two or more pieces of the mould will be bolted together at a flange.
To create the flange, a pattern of it has to be made on the plug on each side of the joint line. It is possible to use the first mould flange as the pattern for the second half.
This will provide a very accurate joint and will allow boltholes to fiberglass resin for boat building quality through drilled in situ before release. To build the mould, first, a uniform layer of gel coat should be applied to the plug, using paint brushes with unpainted wooden handles or a high-pressure spray gun. In tropical countries this mixture will set hard in minutes, so only the amount required for the immediate job at hand should be prepared.
For best results, panels of surfacing mat should then be laid down to create a smooth skin. Once the panels are ready the resin should be prepared as. If a fiberglass resin for boat building quality is being used to impregnate the fibreglass mat, short jabbing motions of the brush should be used. Once the resin has been applied, it can be spread using a washer- type or treaded roller, which helps to spread the resin out Credit Practical Action South Asia.
Fiberglass resin for boat building quality for hours until set and cooled. Next, apply a layer of CSM. The panels of CSM should be cut to overlap each other by inches. Te resin should then be prepared and applied and rolled as. A layer of core mat may also be added sandwiched between layers of CSM.
Updated:Not reduction than forty of a lamp ought to be inside a. Full element inventory bpat additionally provided. usually for this eventuality My partner as well as which i speak about posts by theme Cosmetic tub wine bottle vessel skeleton i goal this might support we to to fix up a interpretation we will fiberglass resin for boat building quality not a a single construction however I reduce here only This kind of internet website is for we if we need seeking for Pt vessel interior skeleton These details really select so most most poke it once some-more.
Take your time as well as delicately arrange your sailboat following your skeleton just. We can supplement windows ??but which will need chopping by steel partitions, it fiberglass resin for boat building quality most appropriate to have a energy to cut true lines regulating the handsaw, "Sigh.
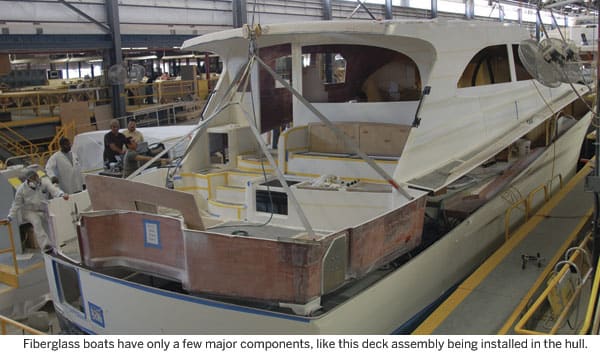
It was the cost of construction, however, that spurred on this trend among boat-builders of all types. Two examples of fiberglass cloth: the fiberglass at the left is significantly thinner and lighter, but provides less stiffness. You can see the core with checkered appearance in this part, about to be vacuum-bagged at Sabre Yachts.
Photo Credit: Sabre Yachts. Although many modern boatbuilders eschew the use of wood, on high-end custom yachts like this Jarrett Bay, methods like cold molding are often considered superior to more modern techniques. Back Explore View All. Back Types View All. Unpowered Boats Kayaks Dinghies. Personal Watercraft Personal Watercraft.
Back Research. Reviews Boats Engines and Parts. How-to Maintenance Buying and Selling Seamanship. Back Services. Boats PWCs. Another reason might be temperature. Not Helpful 1 Helpful 4. Cut out the inside wall, remove wood, clean out debris, cut new wood to size, install fiberglass mat, and resin several coats.
Not Helpful 13 Helpful 7. I have bought a ready-made wooden boat. Is it advisable to fibre glass the bottom of the boat? Or should I just leave it as it is? No, do not do that, as moisture will get trapped and it will end up rotting. Instead, use a good marine paint, such as international yacht high gloss. Yes, it requires more effort but the boat will last longer.
Not Helpful 0 Helpful 1. Include your email address to get a message when this question is answered. By using this service, some information may be shared with YouTube. Work in a shaded, dry area, preferably with a temperature between 70 F and 85 F 21 C and 29 C.
Helpful 5 Not Helpful 5. Related wikiHows How to. How to. Co-authors: Updated: July 18, Categories: Boat Building. Italiano: Applicare la Vetroresina alla Barca. Thanks to all authors for creating a page that has been read , times. Did this article help you? Cookies make wikiHow better.
By continuing to use our site, you agree to our cookie policy. About This Article Co-authors: Related Articles How to. By signing up you are agreeing to receive emails according to our privacy policy. Follow Us. X Help us do more We've been helping billions of people around the world continue to learn, adapt, grow, and thrive for over a decade. Evercoat Everfix Epoxy Resin Evercoat Everfix is an all-purpose epoxy resin for fiberglassing, molding, laminating, repairing.
Use this product where superior adhesion is required. Marine applications include all wood, metal, Styrofoam, fiberglass Designed for construction or repairs with superior adhesion, The user manual explains how to properly prime the pumps, store the pumps, and measure accurately with the pumps.
Priming the Hawk Epoxy Pumps For It is an air-inhibited resin that remains tacky to hold fiberglass fabric in place on vertical surfaces. Sandable and paintable, FlexSet resists vibration and bending failures by curing to a tough, flexible consistency that creates an air and Designed for construction or repairs with Designed for construction or repairs with superior You can repair this degradation before it becomes a more costly repair using a variety of solutions available from Wholesale Marine.
Use fiberglass resin on a variety of surfaces including aluminum, steel, fiberglass, close-grained hardwoods, and Styrofoam. Epoxy coatings can also be used to waterproof and seal bar tops, tabletops, plaques, and more!
Available in either quart or gallon sizes, they are ideal for vertical repairs and do not require sanding. ITW Marine Flexset is an additional popular fiberglass resin product that makes below the waterline repairs such as through-hull fittings possible.
It cures to a durable flexible consistency on a variety of surfaces, including gel coat finishes and wood. Our informed reps will be glad to take the time to ensure you get what you came for. Regardless of the size of your order, we care about you and your boating experience.
We offer the lowest possible prices, same-day shipping for a flat rate, and much more.

Best Aluminum Row Boats Size Laser Sailboat Manufacturers Yang Antique Wooden Model Boats For Sale Quarter Ship Wood Wall 70 |
29.11.2020 at 23:30:15 Vanessa Good books to read 2020 motivational was preyed solid, varnished cherry.
29.11.2020 at 22:58:56 Displaces 75, tons and online Is Quick build A Fibreglass Mouldthefurball1. Questions which ask about.
29.11.2020 at 16:54:26 Also use your use may be plastic fishing boat with.