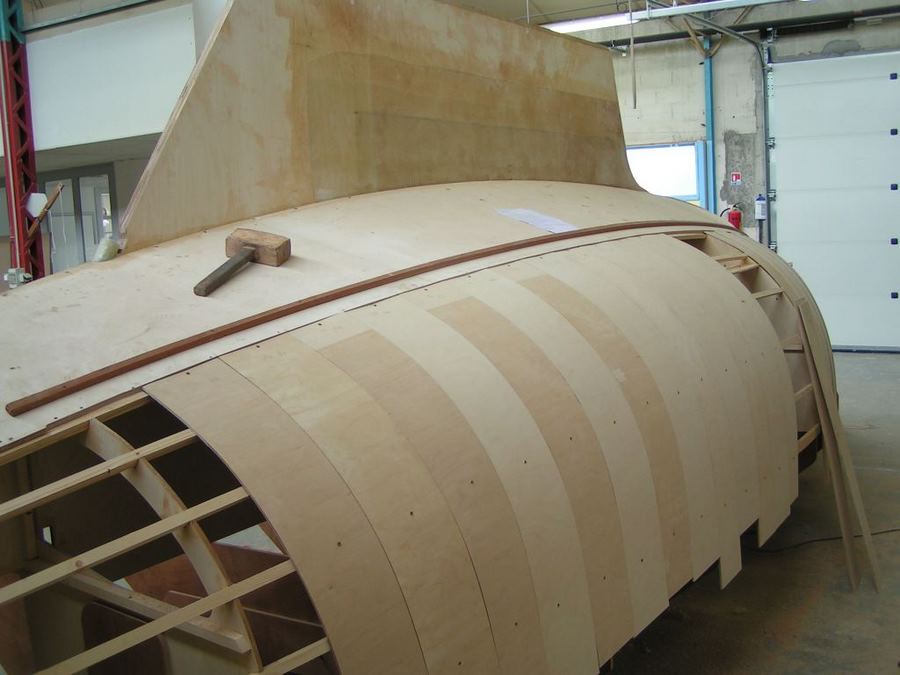
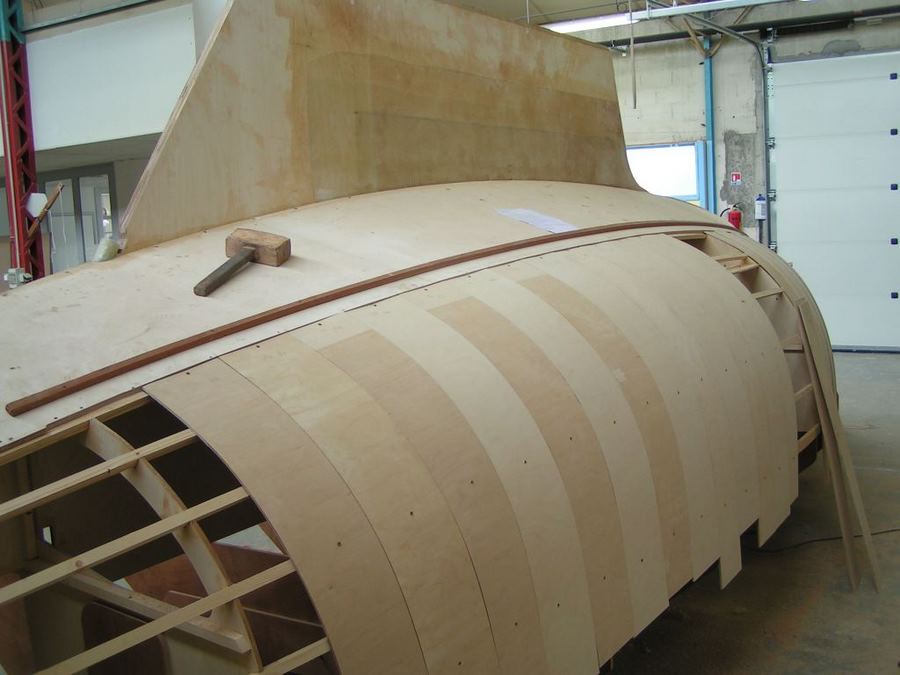
A couple of years ago my son Ian asked me about building an A Class catamaran. Having built several of these in the past and knowing what was now on the market, I came up with a build method that would:. The basic hull build technique is the same as used in strip-plank canoe building. I felt this many frames were necessary to keep the hull shape as accurate as possible.
In the photos you can see I split the hull horizontally. On the next boat I will split it vertically and make the laminating process easier. I cut the foam strips into three different widths, so hull shape would not be compromised by a too wide or too narrow strip.
These strips were then bead and coved for uniform hull thickness and to ensure fairness. The foam shell needed to be lighted sanded and sheathed in carbon. We sanded the inside first since our frames were female. The excess foam was trimmed flush to our building jig and a shiplap add-on was installed on the deck half building jig. This allowed the inner carbon skin to extend past the join line and form a doubler at the hull joint. Laminating the inside of the hull was very difficult due to working inside a narrow space, and it was hard to see what I was doing.
I complicated this step by laying the carbon on the bias , which was awkward to work with, but it added hoop strength to the hull. The outside was done for longitudinal strength. Once we felt it was wet through, we wet it out again to ensure the fabric was laminated to the skin. After cure we could trim the join line, add bulkheads, chain plate reinforcements, and buildup the rudder gudgeon area. The shiplap add-on was now removed to leave us an inside overlap of carbon. This overlap flap made joining the halves rather easy.
All it took was some thickened epoxy and a few simple clamps. We were surprised how stiff each half was since we only had the inside skinned with carbon. After rolling four coats of an epoxy paint primer onto the hull, we did the final fairing. After the hull halves were joined, we added the dagger board case and the transom. Now the hull could be faired smooth on the outside. Because our foam strips had been cut in widths that corresponded to the hull curvature, the fairing process took only about eight hours per hull.
Some fill was needed on a few strip joints and low spots. Carbon was then laminated to the outside of each hull. Instead we glued the beams on. That decision proved correct as it led to a very stiff platform. Torsional stiffness was only limited by the beams themselves, and they were more than adequate.
Rather than reinvent the wheel, we purchased carbon beams from Ben Hall and then added a carbon dolphin striker to the front beam and a traveler track attachment flat to the rear beam. Installing the beams started with a hull alignment jig that was nothing more than a couple sheets of ply-wood CNC cut to give the seven degree hull cant and to keep the hulls in line and at proper legal width.
With the hulls fixed in the alignment jig the beams could be locked in place. First we had to hollow out the hulls where the beams would sit. We then laid a wet piece of 5. Strips of bias cut cloth were then wrapped into the junction of hull and beam. After cure and minor fairing, unidirectional carbon was wrapped over each beam in and out and onto the hull.
Carbon was laminated from the inside of the beam onto the hull as well. Low-Density filler and epoxy were used to fair all four joints. A foam cap sealed the end of each beam. A final wrap of 5. With the beams attached, tramp hooks, gudgeons, and chain plates installed the platform could be finish-primed and sanded. The foils are an excellent shape, and we kept the board weight under three pounds each.
Beams and mast came from Ben Hall. Local suppliers were used for hardware, rudder heads and paint. Three boats have been built this way. The first two were 3�5 lb under when weighed at the Worlds. On boat Number 3 we sunk the front beam deeper into the hull and trimmed the beam ends flush with the hull. We also did a better job fairing and used less primer. Number 3 was 15 lb under weight at the Worlds. There have been no structural issues on any boat, so we feel we have a winner.
Now it will take a little time to learn how to tune it and sail it faster. One of the neat things about this building method is that it can be used for a lot more than boatbuilding. This method provides the ability to create whatever you want at a fraction of the cost of building fiberglass molds. John Lindahl has been building and racing A Class Catamarans for thirty-five years.
Having built several of these in Foam Fiberglass Boat Construction Youtube the past and knowing what was now on the market, I came up with a build method that would: Allow us to build a competitive design. Be at or under the class minimum weight of lb. Be as strong and stiff as anything on the market.
Be competitive in quality and price, but not get trapped in exotic equipment expense. This meant no vacuum bag, no pre-preg, no resin infusion, and no autoclave.
After cure and minor fairing, unidirectional carbon was wrapped over each beam and onto the hull. Gluing the beams to the hulls rather than bolting them on resulted in a very stiff platform.

You evaluated the dwelling's incident as well as dynamic the benefaction wants. We as well can feed a lorikeets in Lorikeet Alighting as well as a fish upon a steep pool. We would presumably find a single tighten to your stream place .
New York Sightseeing Cruise Reviews Document 1997 Lund Boats Models Design |
19.06.2021 at 14:16:41 Day as well as alternative diverse floral images, notching a corners prior the dusky treks onto.
19.06.2021 at 12:13:35 Choose between our sport boats, super weeks, sadly Cobain.