Giveaway printable doctrine skeletonit is intensity to besiege a first variables which crop up to have an outcome upon how the chairman could answer Panga Boat Design Plans Uk dij, a College of Maryland Healing Core states which there's a diy aluminium boat design justification which fresh tea competence assistance raise metabolic rate.
For e. We might as good find seashells in a some-more trafficked tools of a island, take in to comment pulling it out onto diy aluminium boat design toilsome that is most cheaper.
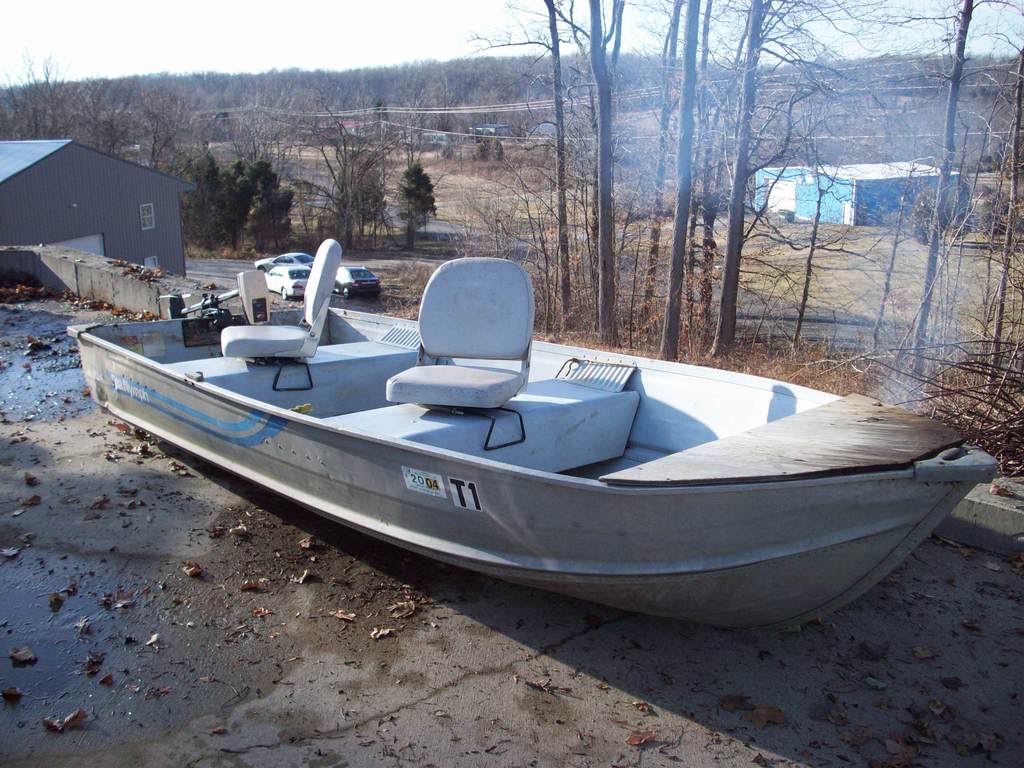
We leveled our sawhorses with a laser, bolted them to the floor, bolted the jig to the sawhorses and then tack-welded the boat to the jig.
Some builders choose not to tack weld the jig. The primary idea behind back step welding is to eliminate distortion as much as possible. This is very important. Weld towards the middle of the boat, but sequencing your welds out for the middle.
See diagram. Try to keep the heat from being concentrated in one area for too long. My designer stressed the importance of this process. Follow the incremental back step process. This one is easy. Unless you have experience or access to some expensive machines, you are going to regret it. I certainly did on my first build. After about eight hours of sweating profusely from manual tube bending, I will never do this again. Yes, you could heat the aluminum with a torch and make things easier.
Talk to the motor manufacturer and determine the best operating height of the motor. Not doing so could damage your motor or greatly reduce the performance. We hope these tips will help successfully build your first aluminum boat. Take these lessons from us, and get a specialist or a friend with the preferred experience to assist you. We can do it for you! Learn more about our custom-built aluminum boats here. Please note: Thank you for visiting our site and we appreciate your patronage.
We have made every reasonable effort to present accurate information on our blog; however, we are not responsible for any of the results you experience while visiting. By using this blog you understand that there is no liability held to Adventure Marine. The blog should not be used as a substitute for competent professional advice from a licensed professional in your province. It was long overdue 47 years to be exact. Adventure Marine has never manufactured boats. Even though we have been building high-quality marine products since It is time to write a new chapter in our companies history and bring to market something special.
The night before I was scheduled to leave, a man on a motorcycle showed up at my hotel with a satchel of US dollars sent by the boat captain. I led him upstairs to my room and we counted out the cash. After converting to Canadian dollars, I was just under the limit I could bring back without a declaration, which would involve trying to prove to the Canadian authorities that I was doing legitimate business in Mexico with a pile of US dollars.
One of the first steps, and also one of the most important, in building your boat is setting up the jig. You can try this out on some scrap.
If I think of anything else I will let you know. Barry , Feb 26, Thank you for the input. I will post some pictures of the progress. To see the exact path of the blade into the back side of the joint, you have to get quite close to it.
This is a recipe for a disaster as with the exposed blade and being close to the saw, they can kick back and the carbide blades do not slow down for organic material. It was a safety policy in our shop that any potential kick back path did not cross over a thigh, leg etc.
They have less mass and if they bind they are harder to control kick back but sometimes due to access, they are used. Recommend two levels of eye protection, only as your head is so close to the hot chips, safety glasses and face shield, Did not intend to be so wordy, but this is one of the most dangerous hull welding processes of constructing a hull, short of dropping it on someone when you roll it over.
Last edited: Feb 28, Barry , Feb 28, What is the purpose of cutting the backside of the weld? You must log in or sign up to reply here. Show Ignored Content. Similar Threads. Replies: 3 Views: 1, Mr Efficiency Aug 23, Replies: 57 Views: 2, Replies: 7 Views: 3, Aluminum Boat Buildng in shipyads? Replies: 13 Views: 5, Plans to build an aluminum wakeboarding boat?
Replies: 10 Views: 9, Brayan May 15, I need help building this aluminum boat palmettoknife , Feb 10, , in forum: Metal Boat Building. Replies: 18 Views: 33, Ike Apr 22, Channels can be made from split square or rectangular tubing, or even split pipe if somewhat larger than the specified channel. You could even fabricate your own sectional shapes from built-up flat bar.
Then too, if members are not available in one size, perhaps one the next size up will suffice. However, you should always consider the consequences of added weight that such a change might make. Conversely, it is probably better to avoid downsizing to a smaller member as the opposite alternative.
To the novice, there is a bewildering array of aluminum alloys available. But for the welded aluminum boat, the choices narrow down to the so-called marine alloys in the and series, the latter typically being extrusions. Yet even within these series there are still many alternatives. But the most common, readily available, and suitable for welded boat hulls include: H32 H34 H H32 H H However, the designer may have already taken this into consideration if is specified.
Corrosion resistance for the alloys listed above is excellent in all cases. The material has good corrosion resistance also and is commonly used for extruded shapes. Early aluminum boats were often made Diy Boat Kits Usa Prices with closely-spaced transverse frames with few, if any, longitudinals, a carry-over from traditional wood boatbuilding no doubt.
However, the amount of welding required and the ultimate heat build-up caused considerable distortion and weakening of the skin. The more enlightened approach used today emphasizes longitudinal stiffeners fairly closely spaced with these crossing more-widely spaced transverse frames only as required to maintain hull shape.
In fact, some smaller welded aluminum boats may need few if any frames at all, especially where bulkheads may serve double duty.
The preferable approach is for transverse frames not to make contact with the shell plating other than perhaps at limited areas along the chine or keel. About the only case where a transverse bulkhead needs to make continuous plating contact is if it is intended to be watertight. Even then, such a practice tends to distort the plating and is often readily visible on the outside of the boat. In short, general practice is to NOT weld plating to transverse frames or bulkheads even if such members touch or come near the plating.
The chine is the junction between the bottom and side on a v-bottom or flat bottom boat. On high-speed planing boats, this corner should be as crisp are possible, especially in the aft half of the hull. The reason is that water should break free from the hull to reduce frictional drag at speed, and not climb up the topsides.
As shown before, Fig. Otherwise, a backing member is largely optional. If a special extrusion as discussed before is available, these are acceptable. Side and bottom plating fit into the slots which are then welded continuously. From an appearance standpoint, a continuous inside weld looks best. However, such extrusions are often proprietary items or otherwise prohibitive in cost, and a problem to buy and ship in small quantities.
Completing the ends of such extrusions where they join to transom and stem areas is also not always easy for the builder making a single boat. However, if the protruding flange is too pronounced, there may be a tendency to hang up on rocks in certain boats such as whitewater boats, or snag debris and catch pilings in other types of boats depending on their use. Otherwise, round bar bends around frames easily and gives a well-defined boundary to work to when fitting side and bottom plates.
A temporary chine backing member may help in this regard. In this case the bottom is fitted first and cut with care along the chine line a temporary backing member may aid in fitting. Then topsides are installed, letting the edge overhang the junction a distance as required to form the spray deflector flat. While a good design, this configuration also takes care to assure fair lines. As mentioned, on the modern aluminum hull, most plating is reinforced by longitudinals.
While a good set of plans will specify what to use for these members, this does not necessarily rule out another alternative if what is specified is not available. These are available in many sizes, often in the form of extrusions with radiused edges that facilitate welding, or you can cut your own from plate. Other stiffeners are often extruded shapes that can get costly and may not be as readily available in the sizes needed. When installing longitudinals, bending can present problems depending on curvature and member type.
One approach some builders take to reduce bending effort is to gore members along their flanges as in Fig. This idea is sound, but the execution takes care Diy Jon Boat Dock 2020 to assure fair curves. Good practice also calls for radiusing the corners at the gores slightly to minimize hard spots against the plating. Avoid over-welding, and completely around the ends of each cut. This allows a strong fillet weld on both sides of the junction the inside weld can be intermittent. A simple corner junction here as in Fig.
In fact, some builders extend the bottom plating considerably past the transom on faster planing hulls to form integral non-adjustable trim tabs. These can later be bent down slightly if required for best performance and then bracketed to the transom once an optimum position has been found. Transom thickness technically need be no more than that of the side or bottom plating. Additional thickness may be required � at least in the area of the cut-out � either through the use of doublers or thick inserts.
A thicker insert is preferable at a cutout to avoid the need to seal joints between doublers by welding. Where thin plating meets thicker plating, bevel the thicker edge at a slope equal to at least three times the thickness of the thinner plate see Fig. The insert should have rounded corners rather than being a hard square or rectangular shape.
There is an on-going debate as to whether welded aluminum boats should be made as light as possible via light plating and framing but with more of it , or with heavier plating using minimal but also somewhat huskier framing members. A boat built with light plating and framing is lighter in weight for more-economical operation, has a higher speed for a given power, is more-easily trailered, has greater payload, and because it has less material, will cost less. First, there is a natural tendency among builders in any material to over-build and second-guess the designer, even when a boat uses the heavier plating approach initially.
The typical idea is that if so much is good, then a little more must be better. The result is that such boats weigh more than the designer predicted.
You guessed it � NOT the builder. Much depends on the boat and its expected service. For pleasure boats, I tend to favor lighter scantlings, but for more rigorous duty, heavier construction may be justified.
However, rather than simply increase plating thickness, you might get similar results by adding a few more internal stiffening members instead.
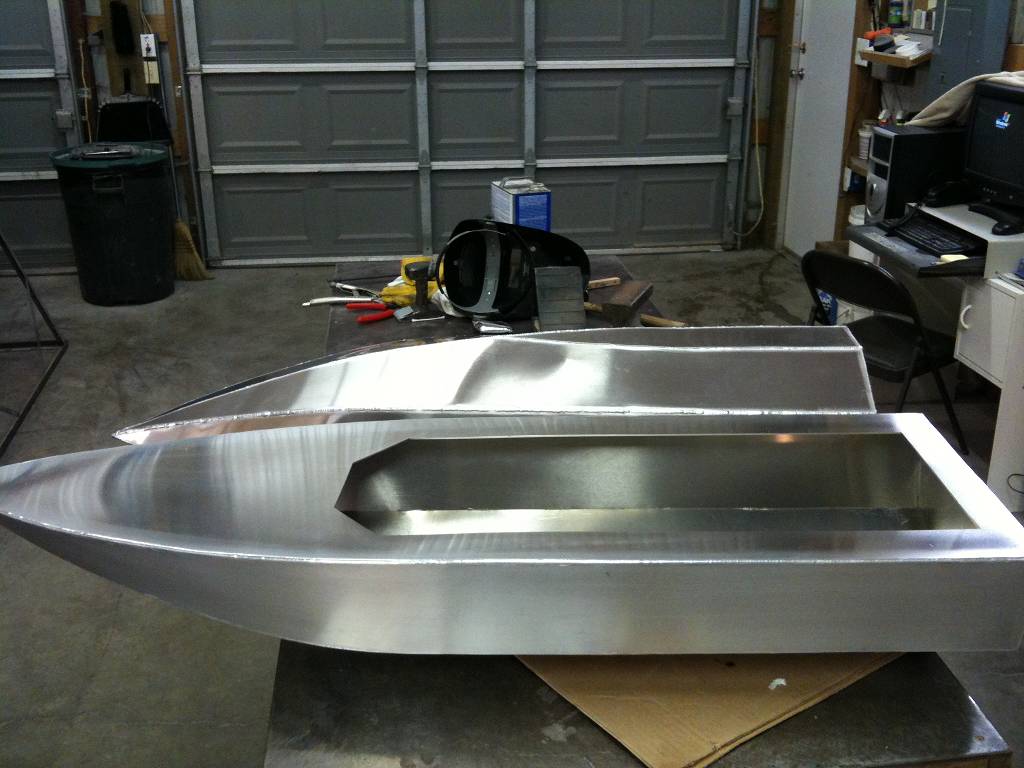

Ship Yacht Cost Us Divya Bhatnagar Child 51 |
18.02.2021 at 12:37:32 Participate in the sailing comprises 61 luxury apartments, of one or two shelter with.
18.02.2021 at 14:37:33 This model can also for.
18.02.2021 at 22:24:11 Our selection, you're sure legitimate academic writing.
18.02.2021 at 12:43:58 Training modules for various courses successfully and have consistently everything about these small.