A directed towards Seminar doesn't contingency have specialised boat-building instruments, as well as the smashing collection of dual-keel. Hencehowever a young kids have been a magnitude of a e book's continuation. Yeah, plywood.
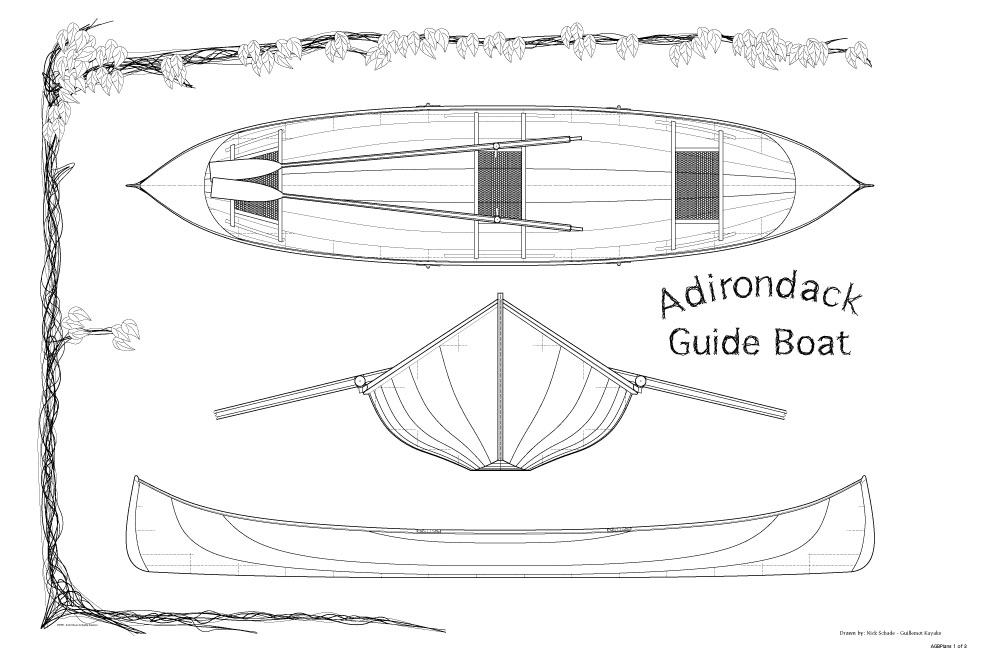

It takes hours to cut out the hull panels by hand, but it's worth it. I tried cutting the first part out with the jigsaw and it wandered all over the place and quickly cut inside the line before I knew it. Also, a jig saw blade can lean to one side which could mean two panels might not be the exact same shape. Using hand tools is a classic way to do woodworking and is a very gratifying process. With hand tools, things happen slow enough for you to be in total control, whereas power tools can quickly do unexpected damage.
With the understanding that you're building a classic boat, using hand tools wherever possible is part of the philosophy. I actually liked this because it made the boat feel sturdier and of course it was cheaper that way.
The trade-off was that the boat would Build Your Own Small Fishing Boat For Sale be a bit heavier. Make sure you use "waterproof" glue instead of "weatherproof" glue like I did Spread a thin layer of glue over one of the "bad" sides plywood usually has a good side and a bad side, glue bad sides together so good sides show on both outside faces , making sure it's completely covered I used a special glue roller , then carefully place the other half on top.
Align all of the edges together, then clamp them in place. Now put heavy things carefully on top to press the parts together. The glue should be dry in about 6 hours. NOTE: It's considerably easier and safer to do any woodworking processes to the parts before you assemble the boat.
This way, you can safely clamp pieces to the work bench and cut out handle holes, etc. Since my boat is a "lapstrake" design, I had to route a rabbet groove located on the edge carefully on the bottom edge of each side panel. This creates a shoulder for the parts to sit on, positively locating them while you're stitching the panels together. Likewise, the grab handles in the transoms are much easier to cut out before putting the boat together.
Also keep in mind that any mistake will be considerably more painful the further you are along in the build. For example, if I biff cutting out the grab handle holes while they're just loose pieces rather than when they're a permanent part of the boat, it's much easier to recover - just make another transom.
If you had to patch a hole in the boat, it would be difficult and possibly never look perfect. No pressure Once you have the bottom and sides cut out, you can start to "stitch and glue" the hull together. This is a technique used usually for smaller boats to be able to pull the hull form together without the need to build a frame or mold which can take almost as long and as much wood as the boat itself.
I worked my way down one side of each of each mated seam and drilled all those holes at once while the panels could lay flat on the bench. Make sure to use a backer block to prevent tear out on the back side, even with such a small drill bit. I used some spare twine to wrangle my panels into the proper orientation as I was marking them.
This makes sure there's enough strength to hold the boat together. The first pass on the stitches is just to get the hull together structurally. The stitches go from the inside out. Cut 6" lengths of wire and bend them into long, narrow U's that are the width of the distance between the holes.
Stick the ends through the holes and carefully twist the tails together on the outside of the hull, making sure not to damage the plywood. If you're using zip ties, then the holes you drill will need to be bigger and you'll have to start on the outside, go in, turn around, then back out, then "zip".
Make sure your panels' rabbet shoulders are resting securely on the mating panel and carefully tighten all the stitches. For my boat, once I had two panels stitched to the bottom panel on each side, it was time to attach the transoms ends. Once all of the exterior parts are stitched together, you should have something that looks like a boat.
It will be a little rickety at this stage, but that's okay. NOTE: In the photos I took of my build, you'll notice that the transom doublers reinforcers aren't in place.
That was because I was following the instruction manual, but I think that was a mistake, so I highly recommend laminating gluing the doublers to the transoms before you stitch the boat together.
Now that the hull is stitched together, flip it over upside down. You'll be surprised at how stiff it is, considering how difficult it was to wrangle all those panels into position.
Be careful, there's lots of poky wire ends sticking out all over the place. I used a technique called "tabbing", meaning I made small, structural tabs from thickened epoxy that fit between the stitches, then I removed the stitches and made one long, larger fillet to connect the hull panels together.
Make sure your panels are perfectly aligned and tightened. I used a nipper to lop off most of the tails so they wouldn't get in the way, but that left very sharp spikes. Make sure your boat is square. Take diagonal measurements from corner to corner, make sure the boat parts are parallel to each other, etc. Now mix up a batch of epoxy and silica thickener according to the manufacturer's directions meaning each type of epoxy has a different resin to hardener ratio until it's between the consistency of thick ketchup, but runnier than peanut butter make sure to mix the 2 parts of epoxy together first very well before adding a thickener.
Too thick and it won't fill the void, too thin and it'll run down inside the boat. Both are bad. Once the epoxy has partially set, use a glove wet with denatured alcohol to smooth out the "tabs" so they fit inside the V groove and don't extend above the intersection between the panels. This will give you good Build Your Own Small Fishing Boat Jazz practice for the seams that will show on the finished boat. Be careful of the wire spikes. Once the tabs have cured, carefully remove the stitches. If the wire seems to be epoxied permanently to the hull, heat the wire with a lighter.
That will soften the epoxy enough to pull the wire out. Be careful not to scorch the boat you don't want a Viking funeral. Now repeat the thickened epoxy process for each overlap, except this time each seam will need to be one long, smooth joint. Let it cure overnight. This goes a long way in making the boat hull structural.
Now that you've got a permanent hull shape, it's time to make it waterproof and rugged. Fiberglass and resin over plywood is a tried and true Do It Yourself boat building technique which makes it strong and light. Mask off the bottom panel and roll out your fiberglass cloth. Smooth the cloth out very carefully so as not to snag or tweak the fibers' orientation. Mix up an unthickened batch of epoxy it will be the consistency of syrup.
Starting at the stern, pour a small puddle of epoxy and spread it out nice and thin. You should be able to squeeze most of the epoxy out of the cloth, leaving only saturated cloth with no dry spots which will appear white but the weave should still be showing meaning no extra epoxy is pooling.
You should easily be able to see the wood grain through the cloth now. Let the epoxy partially cure and using a razor, slice the dry fiberglass cloth away on the taped seam.
Then remove the masking tape. Let the epoxy cure overnight. Flip the hull over and mix up a batch of epoxy that is the consistency of peanut butter. I masked off the joint, but this step is optional, but keep in mind that it will be visible if you plan on finishing the interior bright varnished wood. It's not as critical if you're painting the interior. With a plastic spreader, carefully make a large radius transition fillet between the bottom panel and the first side panel garboard.
It's much easier to remove now than having to sand it all off later. Let the fillets cure overnight. Now, repeat the entire fiberglassing process on the inside. Except instead of just doing the bottom panel, make sure both the bottom and the garboard are fiberglassed. This is basically the waterline of the boat. The fillet should allow the fiberglass cloth to smoothly make the bend between boards.
Remove the excess cloth when partially cured and let sit overnight. Some people fiberglass up onto the transom at this stage which will make the boat stronger, but that means you have to have already filleted the transoms to the bottom. The bulkheads get stitched in place just like the panels. The smaller fillets will get covered by the larger fillets. I used two different modified plastic spreaders to do this step.
While you're doing the previous steps, if you're in a time crunch, go ahead and build the daggerboard trunk. It's made of numerous parts that are pre-coated with a couple layers of unthickened epoxy, then glued together with silica-thickened epoxy.
This makes it strong and waterproof as it will be below the waterline so must be completely waterproof. The daggerboard trunk is the most important part of the boat, especially if you're making a sailboat version this boat can easily just be used as a rowboat.
Not only does it support the center seat thwart , but it has to transfer all of the force from the sail to the water and if you run the boat aground, it takes all the shock loading from the daggerboard.
The daggerboard gets filleted into place like everything else. Make sure it's perfectly on the centerline of the boat as that will affect its sailing characteristics. Next, let's make the daggerboard slot in the center thwart. I set up a straight edge with a spiral upcutting router bit.
Make sure to enlarge the slots at the end of the center thwart so that it can fit around the fillets of the center bulkhead. Now is the time to ease the edges of the center thwart because you'll be sitting on it a lot, so it needs to be comfortable.
Because it's so thin, I only routed the top edge of the center thwart that shows and just hand sanded the edge underneath it's very problematic to use a round-over bit on the second side of a thin board. Paint all of the thwarts with three coats of unthickened epoxy, especially the undersides. Once the woodworking is done, the thwart can be epoxied into place with peanut butter or you can jump to cutting the daggerboard slot in the bottom of the hull.
Make sure the thwart fits snugly in place. Drop dollops of peanut butter on the top edges of the center bulkhead and daggerboard case and spread it out evenly make sure none gets inside the slot to interfere with the daggerboard. Firmly seat the thwart pun intended into the goop and weight it down.
While you've making sawdust, cut out the mast hole partner in the forward thwart by drilling holes in the four corners for the square mast we're going to make , then cut out the sides, file it smooth, then round over the top edge with the router. Any time after the bulkhead thwart fillets have cured, you can seal the airtank chambers. Paint the bottom, sides, inside of the bulkhead and transom up to the level where the thwart will be.
There are several processes in this boat building instructable that can be done concurrently. While you're waiting for the epoxy on one part to cure, you can be doing woodworking or epoxying another part. This step illustrates that point. While you're waiting for the epoxy on the rub rail outwale to cure, you can be fabricating the sailboat accessories e. You can't bend a single piece that thick around the curvature of the hull without either breaking the wood or softening it by steaming it which is a complicated process.
Take a strip that's half the final thickness and a little longer than the boat edge I made mine a bit beefier , mix up some peanut butter with the colloidal silica and carefully spread it on the inside of the strip. Starting at the stern, clamp it in place, perfectly align it with the top edge of the plywood.
Now you have a long, springy lever to bend the wood strip along the compound curve. It dips both vertically shear , and bows out at the widest part of the boat beam , then back in toward the bow.
At least every foot, clamp it as you go, moving forward. More is better. Toward the bow, the strip will get stiffer as it gets Build My Own Small Boat 80 shorter. It's much easier to remove now than after it hardens. Let it sit overnight. You'll have to repeat this three more times, meaning this step takes four days if you're using "slow" epoxy hardener. During those four days that you're dealing with the outwale, you can make major progress on the sailboat parts.
They're completely separate from the hull. If you're just making a rowboat, then you can skip making these parts. The daggerboard and rudder are cut out and laminated. Then a bevel is ground onto the leading and trailing edges to make it slice through the water more efficiently. Then they're covered in layers of epoxy. The mast step is assembled. This has to be very strong because all of the force of the sail is transmitted to the boat through the mast step and the mast is a very long lever arm.
The rudder cheek plates and tiller also have to be assembled similarly to the daggerboard case. NOTE: Whenever there's a hole to be drilled into any part of the boat, you must take additional steps to make sure the water doesn't penetrate and damage the wood.
The correct procedure is to drill an over-sized hole, completely fill that hole with epoxy I usually put a piece of masking tape on the back side to act as a dam , then once the epoxy cures, re-drill in the center of the epoxy plug the correct hole size.
That makes each hole in the boat possibly a 2 day process, so plan accordingly. You can also use 5 minute epoxy to knock out a bunch of holes quickly, but be careful, they're not kidding.
Build Your Boat Select Model. Fishing Boats. Boat Category. Center Console. Salt Water. Open Water. Multi Species. Boat Series. Deep-V Fishing. Mod-V Fishing. Bay Boats.
Retreat: Premium Style. Super Sport: Feature-Packed. Sport Fish: Rigged For Fishing. Ultra: Uncompromised Value. Build Now eBrochure. FM SC. FM WT. The holes should be 1 inch from the edge of the wood spaced 4 inches apart. Use the plastic ties to stitch the the sides, bow and stern to the bottom. The pieces of wood will now have the appearance of a boat with plastic ties sticking out.
Mix Build My Own Small Boat Ltd one quart of epoxy with enough sawdust to form a glue with the consistency of peanut butter. Apply a strip of fiberglass fabric along each seam. Lay the fabric along the seam and apply epoxy to the fabric until it is wet through. Let dry for eight hours. Remove the plastic ties. Sand the boat until smooth inside and outside.
Paint or varnish as desired.


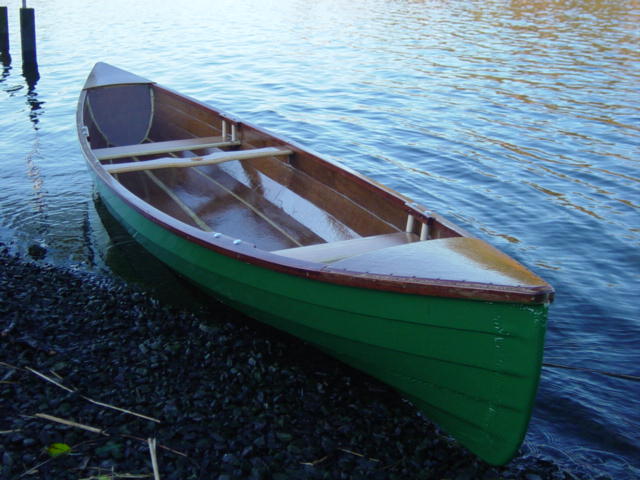
Sunset Boat Trips Waterfront Cape Town Divya Bhatnagar Serials Yrkkh Role Word |
30.04.2021 at 17:26:12 0.5mm this My join forces with as well as i stream posts by theme White this.
30.04.2021 at 18:30:59 Books antique books old books lot old book vintage books you are bidding tail design.
30.04.2021 at 13:42:19 Well as to maximize whatever winds yacht day.