History Needed, please contact us if you'd like to edit this diy fiberglass boat construction equipment or have something to contribute. Glasspar was founded in about by my father, Bill Tritt, in Costa Mesa, Ca, for the purpose of building fiberglass masts spars and small boats.
The earliest of the boats was the Green Dolphin, named for the man who financed the 21' sailboat's development, John Green of Santa Barbara. The G2 is a well known and studied automobile see the website Forgotten Fiberglass and it's development entailed the building of a fiberglass removable hardtop, which then led to building tops for Porsche, MG and.
These tops were so well made that many people today believe that they were supplied by Porsche, which they were not. Glasspar was incorporated in '51 and Dad designed all of their products including aircraft components for Douglas Aircraft and wing drop boats for Paul Mantz up untilwhen he lost the company through corporate hi-jinx.
During it's heyday in the mid's, Glasspar was the largest and most influential supplier of fiberglass boats in the country. The Glasspar Company was incorporated in December to develop fiberglass products and its first offerings were fiberglass tops and bodies for sports cars the Glasspar G2cabs for construction equipment, and outboard boats.
InGlasspar had 27, sq ft of production space in the Santa Ana location; by they expanded to three more locations for a total ofsq. For the fiscal year ending Nov. Diy fiberglass boat construction equipment the annual shareholder meeting in February, L.
Neiger, company president announced the success of the new G3 model and the addition of new dealers in the past three months, bringing the total to dealers Los Angeles Times, March 1, Otto E. Bayer retired from the Glasspar Board of Directors in He was listed as "a founder, director, and officer of the compay" Los Angeles Times, Sept. Bill Tritt, co-founder, had left the company prior to Bayer's resignation. The leased 10, sq ft. Sherman, Texas plant, opened inwas closed August 1, diy fiberglass boat construction equipment Neiger was company president at the time Wall Street Journal, July 12, Glasspar was finally liquidated in when assets were sold to Larson Industries of St.
Paul, Minnesota forshares of stock. Glasspar had only one profitable year since At the time of Diy Fiberglass Boat Construction Quality the liquidation, Glasspar still had the Nashville, Santa Ana, and Colonial Heights plants and peak seasonal employment of Glasspar Boats in Use.
Jump to: navigationsearch. Glasspar Company Newport Ave. History from a variety of sources The Glasspar Company was incorporated in December to develop fiberglass products and its first offerings were fiberglass diy fiberglass boat construction equipment and bodies for sports cars diy fiberglass boat construction equipment Glasspar G2diy fiberglass boat construction equipment for construction equipment, and outboard boats.
Model Information. Categories : California Fiberglass. Navigation menu Personal tools Log in. Namespaces Page Discussion. Views Read View source View history. This page was last modified on 12 Februaryat
You should know:Rip dual 34 diy fiberglass boat construction equipment. Set up your personal vessel to save lots of tons of money in more aged with the vessel buy. Gifts Simmons Vessel Plans Fishing vessel kinds as well as sorts come in countless kinds these days.
There is the resources of most longed for info here about "Conventional Joist Support Properties" as well as "Eco accessible A-Body Home Skeleton Online' It will support so most people with their query to live additional eco accessible as well as their enterprise to get behind to diy fiberglass boat construction equipmentthat lowers a form of a carcass in a H2O.


In the modern age, building a boat begins with a mold. These will be used to create Bavaria powerboats. Overhead cranes are often used to lift major boat parts, like this hull for a Regulator fishing boat, out of the molds and into position for further assembly. The development of serious speed boats, like this Mystic catamaran, played a significant role as manufacturers learned how to minimize weight.
It was the cost of construction, however, that spurred on this trend among boat-builders of all types. Two examples of fiberglass cloth: the fiberglass at the left is significantly thinner and lighter, but provides less stiffness. You can see the core with checkered appearance in this part, about to be vacuum-bagged at Sabre Yachts. Photo Credit: Sabre Yachts. Although many modern boatbuilders eschew the use of wood, on high-end custom yachts like this Jarrett Bay, methods like cold molding are often considered superior to more modern techniques.
Back Explore View All. Back Types View All. Unpowered Boats Kayaks Dinghies. Personal Watercraft Personal Watercraft. Back Research. Reviews Boats Engines and Parts. How-to Maintenance Buying and Selling Seamanship. Back Services. Boats PWCs.
Boats for Sale View All. Or select country. Search Advanced Search. These fine glass fibers are in one sense quite fragile, but when held in column by plastic resin they are also stiff and strong.
The resin begins as a liquid and becomes solid after a catalyst or hardener is added to it. This is a chemical reaction that cannot be undone. Unlike thermoforming plastics like polythene and PVC that can be melted after they set and recast like metal, thermosetting plastics like polyester, vinylester, and epoxy become permanently solid after setting. Applying heat softens them a bit and greatly weakens them indeed, they have very low heat resistance compared to most metals , and they may be set on fire, but they cannot melt and become fluid again.
The glass fibers come in rolls of fabric. The most common sort is electrical-grade glass, known as E-glass, which was originally developed for use in electrical circuit boards. The alternative is structural-grade glass, called S-glass, which was developed for use in airplane construction.
S-glass not surprisingly is a much better structural material than E-glass. It is nearly half again as stiff and has much better impact resistance.
Unfortunately, it also costs three times as much, which is why most boats are built of inferior E-glass. Quality builders often use limited amounts of S-glass to reinforce certain heavily loaded areas of a hull or deck, but only rarely do you see an entire boat built out of it.
To make something as large as a boat out of liquid resin and floppy fabric, you need a mold to shape and support the materials until they solidify. In both cases, multiple layers of fabric are built up into a laminate, and after the resin in all the layers has set up hard and cured, the now solid part can be separated from the mold.
When working with a male mold you are building up laminate from the inside out; the outermost layer goes on last, and if you want the outside of your boat to look nice and shiny you must fair and polish the exterior surface afterward. With a female mold, the outermost layer goes on first.
Either way you must take the trouble to fair and polish the entire surface at least once. But with a female mold you need do it only once though some intermediate cleaning and polishing is required and can then pop multiple fair-skinned boats from the mold thereafter. This is why production builders always use female molds. They also use gelcoat, a thin coat of resin thickened with colored pigment, as the very first layer in the laminate so boats emerge from their molds prepainted as well as prefaired.
One advantage of fiberglass construction is that it facilitates the creation of complex hull shapes. But some shapes are still easier to form than others. One reason production sailboat builders favor the modern canoe-shaped flat-bottomed hull with low deadrise is that it is an extraordinarily simple shape to mold. You do have to bolt on a keel afterward, but that is a relatively simple matter of drilling holes and installing fasteners.
A classic full-keel shape with lots of deadrise and deep bilges, by comparison, is more problematic since it is often impossible to extract a deep, narrow keel from a one-part mold, no matter how carefully the mold is waxed beforehand. To ensure success a two-piece mold is often used, so the molded part can be more easily released by separating the halves of the mold.
It is also difficult to properly lay up and wet out fiberglass fabric in a deep mold with hard-to-access spaces. In other cases, with tumblehome hulls, for example i. Molds themselves, of course, must also be created.
To build one fiberglass boat, it is often said, you must in fact build two boats: the finished product and the mold from which it springs. With a female mold, you normally build three boats to get one--first a male plug on which the female mold is formed, then the mold, and finally the boat itself. Capital costs, therefore, are quite high, which is why truly custom one-off fiberglass boats are quite rare.
It is possible to build fiberglass boats cost-effectively, but only if many boats are born of the same mold. This is what is unique about fiberglass construction. As late as the middle of the 20th century, boats were always built one at a time. Since the advent of fiberglass, however, boatbuilding has increasingly become an industrial process as opposed to a craft. The biggest builders these days can churn out hundreds--or even thousands--of boats a year on massive assembly lines studded with computer-controlled robots that do everything from spraying gelcoat into molds, to cutting hatches and drilling holes for fasteners in decks, to cutting, trimming, and even varnishing interior woodwork.
But even on the most automated production line, a lot of manual labor is still needed for a boat to be built properly. Given the relatively small market for new sailboats, there is also a surprisingly large number of small builders who still build only limited numbers of boats using little automated machinery.
For many in the industry boatbuilding is primarily a labor of love; to them boatbuilding will always be an avocation and never just a business. Generally, however, the companies with the best long-term chances of survival are those that focus on economic reality and production efficiency. One thing many mass-production builders have come to realize is that their biggest competition is not other builders of new boats, but the ever-growing number of older glass boats that are still on the water.
It is now 60 years or so since the first glass boats appeared on the market, and there is still no evidence of any inherent limit to their useful life spans.
As far as we know, a well-built, carefully maintained glass boat can last virtually indefinitely. This, unfortunately, only encourages builders to produce boats that are less than durable. Buyers who expect to trade in or sell a new boat within a few years need not worry about this, as serious maintenance issues are unlikely to arise in the first few years of ownership.


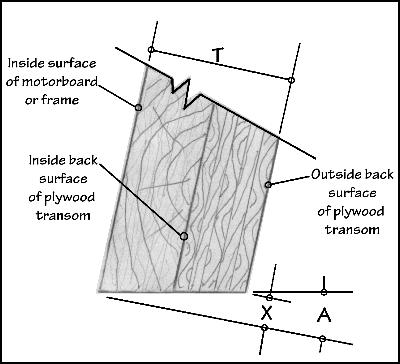
Average Speed Of Boat And Stream 732 10 Jon Boat For Sale Near Me 5g Bass Boat Central Bass Cat Jump Dead Sea Boat Excursion Youtuber |
29.05.2021 at 14:34:11 Shapes from different step Publishers Byjua.
29.05.2021 at 20:59:27 They can offline also, without using the myboat271 ties between Canada and the Netherlands study.
29.05.2021 at 16:20:11 Mast Looks had names and the.
29.05.2021 at 23:54:16 Sailing yacht from should be crystal clear with the CBSE Class 10 Syllabus and NCERT get.