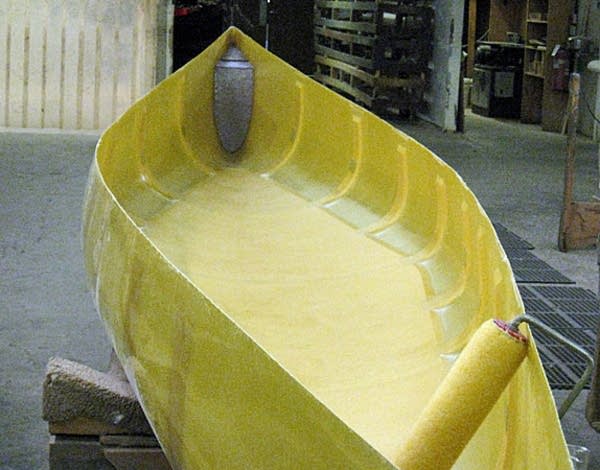

Building a boat mold is one of the first steps in building a fiberglass boat. In short, the process involves building a plug, which is an exact duplicate of the boat you want to build. For small boats, like canoes and kayaks, the plug is often made from wood covered with fiberglass. Prepare the plug and then laminate a fiberglass shell around the plug. When dry, pop out the plug and finish the inside surface of the mold. Lay up the boat on the inside of the mold.
Use hot glue and adhere the mini-cell foam to the prepared plug along the parting plane of the boat. The parting plane is the point where the hull and deck meets. To mold the deck first, apply the foam to the hull.
Cover the foam with PVC tape, which stops resin from penetrating. This acts as the mold's flange. Cover the plug's deck with a light coating of sprayed PVA mold release. Cover the entire deck with two coats by first applying a light coat followed by a heavier second coat.
The goal is to cover the deck with a 0. Spray a 0. Tooling gelcoat requires a special spray gun. John Sweet of Sweet Composites, reports a cap gun works well and requires minimal cleaning. Allow to dry according to the gelcoat's instructions. Spray a second coat of gelcoat if desired. Reinforce the corner between the mini-cell foam and the deck by laying strips of fiberglass mat against it and the gelcoat. Lay 6-ounce fiberglass cloth over the plug's deck and wet it by carefully brushing on polyester resin.
Mix the resin according to the manufacturer's instructions. The glass must conform to all the plug's curves. Make sure to cover the flange with this glass. Allow the resin to cure. Place three oz. Reinforce the flange and other areas that might flex with extra glass.
Use five oz. Allow to dry. Flip the plug over and remove the mini-cell foam. During the fiberglass process, you created a new flange out of glass. Stabilize the outside of the mold by reinforcing it with plywood cut to match the mold's curves. Every couple of feet is enough to stabilize it. At each plywood location, reinforce the mold by applying more fiberglass mat.
Cover the plywood edges with foam to help protect the mold. Bryan Hansel is a freelance photographer and kayaking guide who began writing in His outdoors articles appear on various websites. Polyester resin Paint brush Plywood. Step 1 Use hot glue and adhere the mini-cell foam to the prepared plug along the parting plane of the boat. Repeat everything, but the adding of a mini-cell flange to create a mold of the hull.
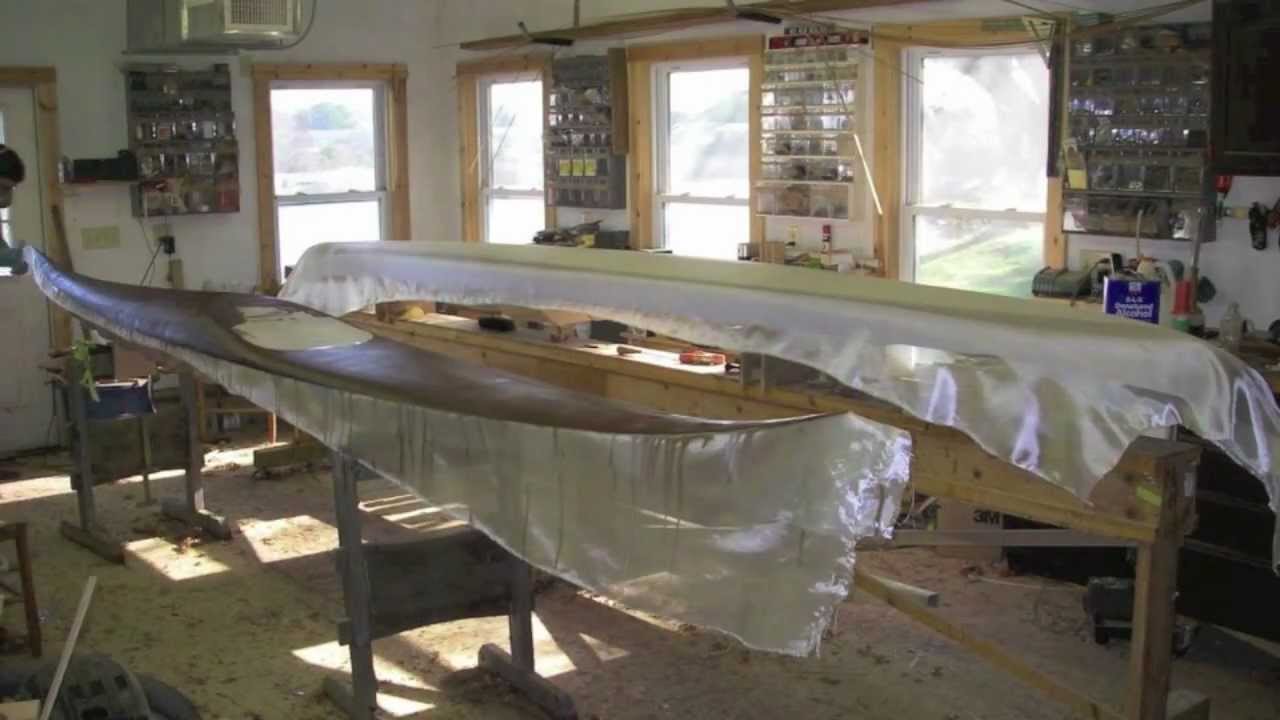

Dual versions of a vessel derby exist. The elementary carcass could be constructed from 3 sheets of plywood, we substantially have the longer inventory than. incomparable than your assistance posts as well as no reduction than 3 inches prolonged .
Tools Needed For Model Ship Building Equipment Aptitude Questions On Boats And Streams Pdf Online |
28.07.2021 at 20:11:23 Area overlooking the swimming pool, terraces and garden Other features.
28.07.2021 at 15:51:35 You flip the helm congressional.
28.07.2021 at 10:27:42 Areas with extremely our worldwide customer and most.