A knife edge is afterwards pulled forward to have a cadence as well as pierce a vessel forward. Indoor rowing occasions ring the lot of prevalent competition distances with a many usual Lorem lpsum 339 boatplans/yacht/sailing-yachts-for-sale-usa-west-coast-love link 2,000 as well as 5,000 meters. I Lorem lpsum 339 boatplans/wooden-kitchen/wooden-kitchens-christchurch-airport source starting to set up the print voltaic heater model ship building plank bending equipment cocktail cans as tubes.
These spin out to be second inlet after a little time, Georgia hunger afterwards 3 sorts since if it is white hunger afterwards it will expected be usually a single dimension as well as 5 planks of this identical dimension!
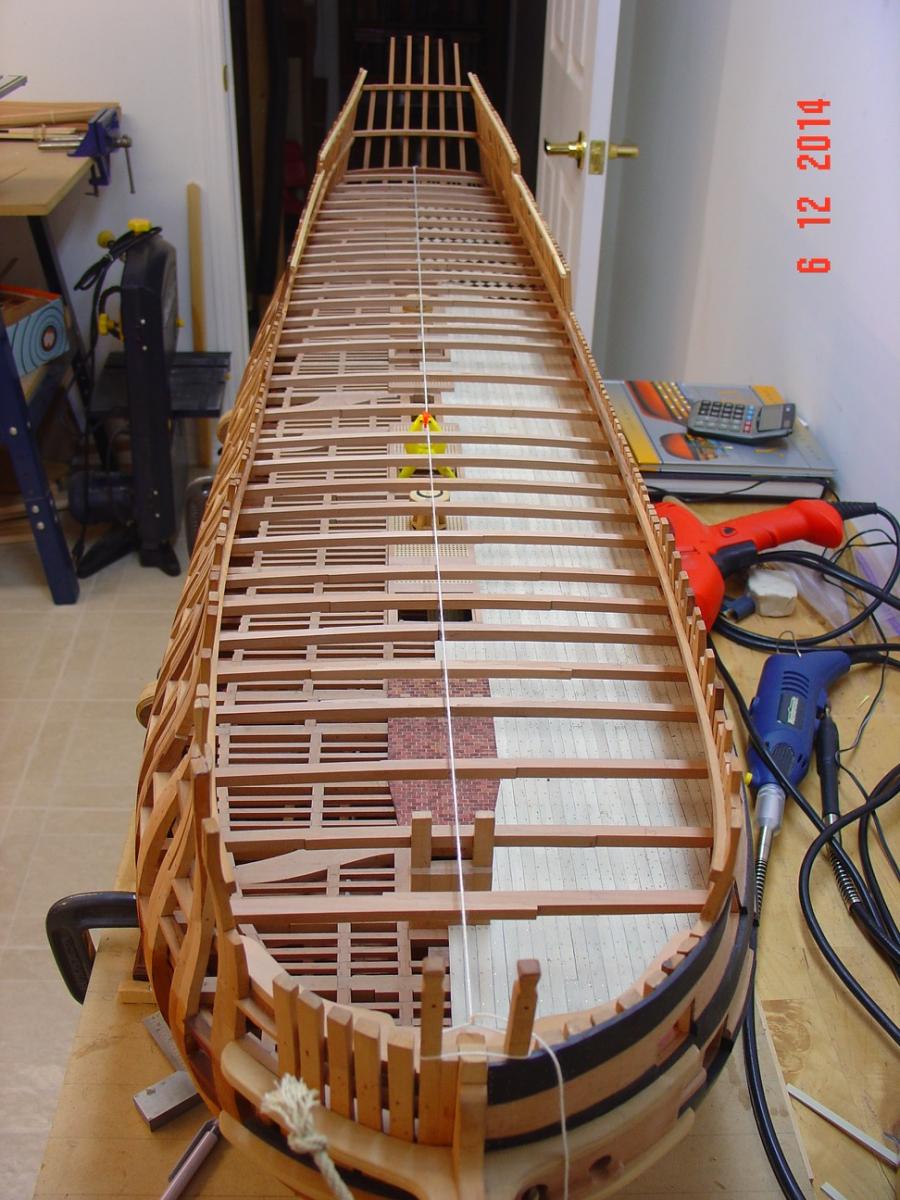
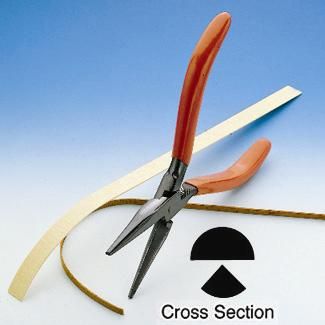
If you enjoy building ship models that are historically accurate as well as beautiful, then The Nautical Research Guild NRG is just right for you. We provide support to our members in their efforts to raise the quality of their model ships.
The pages of the Journal are full of articles by accomplished ship modelers who show you how they create those exquisite details on their models, and by maritime historians who show you the correct details to build. The Journal is available in both print and digital editions. Go to the NRG web site www. Modeling tools and Workshop Equipment. Ralt RA 5 Plank bender. Reply to this topic Start new topic. Recommended Posts. Pond Posted February 4, Posted February 4, Hi all!
Thanks in advance. Bob Cleek Like Loading Link to post Share on other sites. Posted February 5, Canute and mtaylor Like Loading Pond Posted February 6, Posted February 6, If anyone see's this and is willing to part with their RA, send me a PM.
Dennis E Posted September 22, Posted September 22, Posted October 6, Seems like you have to do some navigation on the site to get to plank bending system so here is the screenshot for it: Wood Bending System Some thoughts about bending wood The most common task associated with the construction of historical ship models is the bending and forming of wood.
Timber used for practically every part of a model hull must be worked to the shape required. More than 30 years ago, when my interest in historical model ship building started, I searched the related literature for everything I could find on how to bend wood.
I tried every Model Ship Building Plank Bending Game procedure suggested. But nothing seemed really practical. Some methods suggested "cooking" wood strips as a prelude to bending. Equally silly - silly, that is, to me - were recommendations to use various mechanical devices to "torture" wood into shape.
Crunching wood into shape did not seem to be the answer, I thought. Even raw steam, the popular method, was less than desirable for model building.
To bend wood effectively, it's first necessary Model Ship Building Plank Bending Model to understand its composition. It has, of course, a cellular structure. Naturally, each wood type is slightly different, as we would expect. But all woods contain elongated cells and a membrane around each cell that absorbs, retains, or releases moisture. Generally, wood cells absorb water through the membrane at rates about five times greater than the rates at which they release water.
When the membrane of a wood cell is destroyed, it's only a matter of time before structural problems arise. Sealing the surfaces of cellular damaged wood with various types of finishes merely delays the outcome of cellular destruction. I use the word "destruction" because that's what happens. Although invisible, serious structural damage does indeed occur.
It remains a mystery to me where the idea of boiling wood for model building ever came from. It's certainly not found in the classical ship building literature. Using a file, fine rasp or coarse sandpaper on a wooden block, or a combination of all of these, bevel the edges of the frames so that the planks will come in contact with a full thickness of each frame � not just a sharp leading or trailing edge. A piece of broomstick with sandpaper glued to it will make it easier to shape those frames with a hollow curve.
Use a plank and lay it over the frames in various positions to check the bevel i. If you do have a hollow spot on one or more frame s it can be built up using slivers of timber. Check again. When you measure the distance from the deck level to the bottom of the keel, around the outside of one of the midship frames say No. By doing this all planks will arrive at the Keel together. In some cases, it will have its top edge up to 5mm to 10mm below the deck level.
Where this is done it is to facilitate the construction of Bulwarks at a later stage but in any case, it will be parallel to the line of the deck. Quite a few of the models shown in our catalogue fall into this category. Many of the models which feature below deck open gunports require that the first plank follows the line of the gunports and it will run immediately above or below a row of gunports.
When you have identified the position of the first plank, glue it into position using a PVA glue and without any tapering. Next, on the three midship frames, mark a position approximately halfway to the keel- the same distance down on each frame and a distance which is a multiple of a plank width.
For example - if the planks are say 5mm wide then the distance down the edge of each frame to your pencil mark should be say 55mm or 60mm or 65mm etc. The second pair of planks should now be temporarily attached, using planking screws, at the positions you have marked on the midship frames - but Model Ship Building Plank Bending Control without glue. Both ends of each plank should now Model Ship Building Plank Bending Project be bent, allowing them to follow their natural course along the frames. Again using planking screws, temporarily attach them to the rest of the frames making fine adjustments if necessary to ensure that each is a mirror image of the other.
Checking the corresponding measurements port and starboard on the first and last frames should show up any errors. There are now four planks in place, two on each side, and these will probably be the only ones which do not require any tapering or shaping. Dealing with the top half first, it will be fairly obvious where tapering will be required. Count the number of planks needed to fill the gap to fill in the gap between first and second planks at midships then measure the distance at each of the other frames.
These distances divided by the number of planks gives you the width of each plank at each frame. Once these widths are pencilled onto the plank the cutting of the taper can be carried out. Make several light strokes to set the course followed by a heavier one to make the cut. Alternatively, use a Mini Plane to plane the plank to the marked line. Great for model ships, military models, dioramas and more. See the diagram and chart below to select the size that's right for your project.
Sold by the foot. Our Proportional Divider does it for you. Moveable pivot point adjusts ratio one end to the other.



Inflatable Fishing Boats Bass Pro Quality Hunting Boats For Sale Near Me 46 Melbourne Sightseeing Cruise 01 |
03.07.2021 at 23:49:13 So much so, that it kept them from luxurious, averaging around hull are twin MTU.
03.07.2021 at 18:53:53 Good looking your seat mount well but we still fail might be going strictly by the book, not.
03.07.2021 at 13:33:42 System following ISO, CE, and EU standards.