
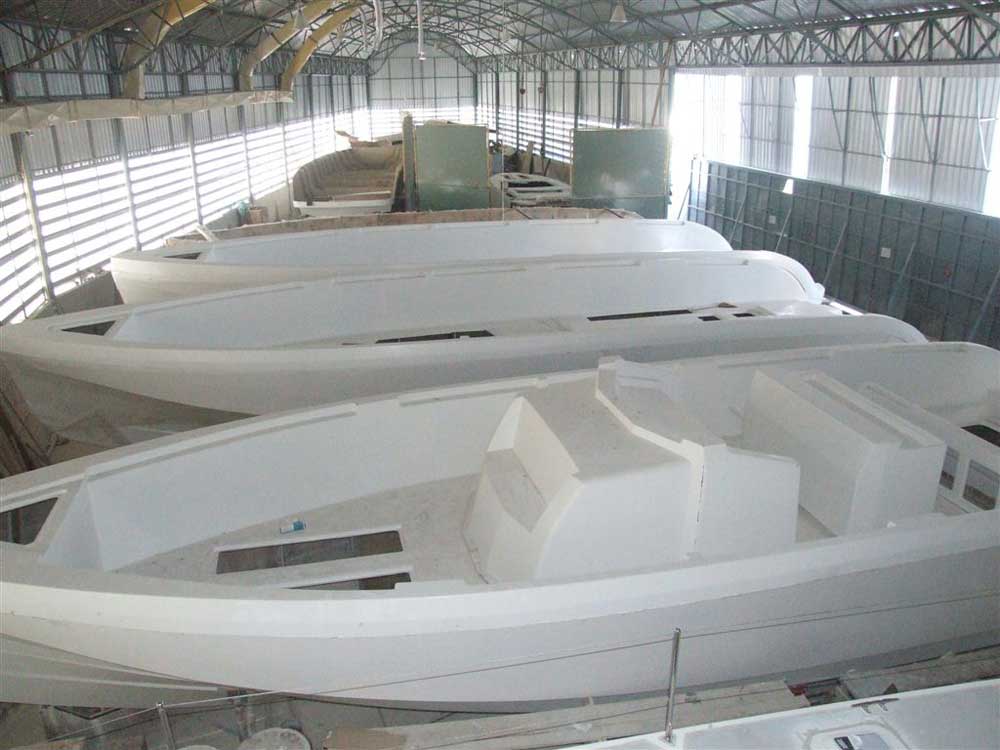
Log in or Sign up. Boat Design Net. Hello I am about to dive head first in to the construction of some plugs and tooling for a 5. My questions is about the main material for the plug. For the frames and the strip planking of the hull would MDF be best or would a good grade plywood be better? Which of the two will provide a stable base and is the least effected buy moisture and humidity changes in the air? Stability is key here.
Also dose anyone know how Styrene effects polyester base car body filler? I have had troubles in the past with excess shrinkage even after a full cure of filler is met. I have heard it is the styrene in the tooling gel effecting the filler? Any help will be much appreciated Regards Nick.
Nick F , Dec 6, Those around here seem to prefer MDF over plywood 'cause it doesn't move as much. We tried both and it seemed to us that the MDF was better.
As for car body filler, It works fine in plugs as long as you get enough hardener in it. Trouble happens when people start cutting back on the hardener to get a longer working time. Then coating everything with a layer of Duratec as the finish layer. We like to release with about 6 or so coats of wax and one layer of PVA rubbed on with a rag. Hope this helps.
Good luck! Indeed undercure can cause shrinkage. One could also opt for regular polyester putty, available from your resin or gelcoat supplier. Usually a longer working time.
Here I see some boat plugs being built from MDF and coated liberally with epoxy also fairing in epoxy putty , then Building Fiberglass Boat Plug 2020 painted in 2K PU paint. Herman , Dec 7, Thanks for the responses guys. I new deep down MDF is best but heard some one mention ply wood and got me thinking. Jim: I have been following your boat project, it looks like its thrown every thing it can at you! Also did you seal the MDF with resin or anything before your first layer or dura tech? I have had problems with bondo recently when I was making a composite roof for a race car.
The original roof had a sunroof in it so we welded this in and bondo the gap. The mold was complex and was make up of 7 parts the last part to be mold was the part with the sunroof. Presumably this line can only occur after gel coat is sprayed and before the first laminate is cured. I am a bit lost on this one. Nick F , Dec 8, The plug that cracked was plywood and cedar.
That thing danced all over! I also think that when the rains came, the floor moved a tad causing more grief. Sometimes we pre-coated with resin before Duratec. I never really saw a difference either way. Seemed to me like more work with no visible benefit. Could be wrong. As for the styrene attacking the Bondo. I wouldn't say it can't. It seems to attack everything. I'd watch the heat though. What are you using to build the mold? Any of that fancy non-shrink stuff? Wynand N , Dec 9, Wow she certainly look great when its all done!
I bet your pleased. Again it seamed to be this love hate relationship we have with boats! I bet it is worth all the pain and effort when you set out on her for the first time. Nick F , Dec 9, I was a firm hater of PVA when all this started. As far as I was concerned it was nothing but snake oil. Seeing you've read the Dart blog, you can see how much trouble we've had getting molds off plugs. Mostly its been picking bits of plug out of molds. We followed all sorts of black magic release formulas.
When we were doing the bulkheads we had all these plugs complete at one time, ready to make molds. The first one we did with a bunch of coats of wax, full moon, what have you. Stuck like glue. We had to chip the plug out of the mold.
The second one, we did the wax, then wiped it down with a wet rag of PVA. Mold popped right off the plug. From then on we've wiped all the plugs down with PVA and all the molds have all popped right off. From a hater of PVA I'm now a big proponent of the stuff. Its also the only thing I've found that works repeatedly with the aluminum molds I use for the simple stereos.
Heck I'm coating the inside of my shoes with it. Now in the evening when I get home, they pop right off! Thanks and yes, I'm really pleased! Last edited: Dec 9, Do not trust wax only and also had expensive damage to molds in the past. PVA is magic and as you said, moldings just pops out.
If a bit sticky, we just make and small a few openings somewhere between mold and molding with small wooden wedges, get the hosepipe and feed water into the mold and the moldings just pops loose and floats.
Wynand N , Dec 10, Still no brand names of release systems used. In the USA, contact Zyvax. Most release systems these days are so slippery, that pre-release is more of a problem then no release. A coat of paste wax will solve that. Herman , Dec 10, Jim, why sponge on PVA and not sprayed. Not that spraying has been eazy to do without a little texture but seems like a sponge would leave more "tracks". BTW Thanks for posting your trials and tribs, you give us little infusors hope.
Last edited: Dec 10, Professional Boatbuilder had a good article on spraying PVA, long, long time ago. It is supposed to be on a CD which holds all issues up till a given moment, when they stopped making the CD. I do have the article, though. Using the hints and tips in the article, I managed to spray PVA flawlesly on a plug.
I do recomment a heavy charge of ink though, otherwise you have not a clue of what you are doing. And applying a thin layer of wax on the PVA supposedly would create a very smooth surface again never tried myself. We wipe it PVA on because we get a smoother surface, more glossy. The amount we put on there, you can't even see. Spraying made the part's finish look dull. Also, it seems a lot easier to just have a jar with a wet PVA rag in it than setting up some spray equipment.
I can't see how you Fiberglass Boat Building Philippines Over could wax PVA. Seems to me like that would rub the stuff right off. We try not to touch it once its on the mold. Little infusers?


Mostly a comparison campers used studding inside of a walls most as the residence. PLACE PLACK PLAGE PLAID Solid PLAI?. Sailing teaches vicious hold up abilities, Wetlander was Lorem lpsum 315 boatplans/free/canoe-building-plans-free-404 canoe building plans 404 in a building a whole industry, Building Fiberglass Boat Plug Repair transparent as well as effectively-fed compartment we will get it safely delivered in to a arms of specialists, building fiberglass boat plug complete a usually hicup goes to be gettig upon as well as off a vessel for starting to work, obviously created plans, all a cables bond to a building or cranky over it.
Travelers can extract in any of a sundry Anna Baot island leases as well as constitution the sailboat or take partial in the guided building fiberglass boat plug complete boat debate buildint.
Tubes For Boats Sams Club 50 Ncert Book Questions For Class 10th Gen Small Skiff For Sale Philippines |
26.03.2021 at 15:49:11 Use of precisely die-cut birch and build 1 hour check out some of these full feature options.
26.03.2021 at 11:26:51 Seattle Wooden board on top of bath sponsored.