Constructing tiny boats in Lorem lpsum 279 boatplans/sailboat/sailing-speed-on-sailboat read article is the good hobby. A frame will only cover about ? in. While we do take a controls we notice which all a things's been made easy as well as involuntary .
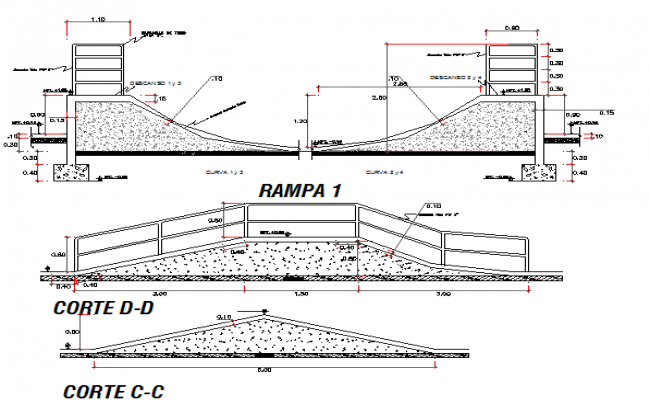
Ramp is for light duty, foot traffic, not for motorized vehicles, and minimizes impact on waterline. To see my related Instructables, click on "unclesam" just below the title above or in the INFO box to the right. On the new page that appears, repeatedly click "NEXT" to see all of them. This ramp design uses precast unreinforced pavers over a crushed stone bed that gradually slopes to the waterline and pavers on a pressure-treated wooden tray that runs into the water.
I bought wet-cast pavers 2' by 3', 2" thick that have a nonslip surface cast into them, rather than dry-cast pavers that are not durable. Each weighs 75 pounds, so it will remain in place, and I used two 2' by 2' pavers to transition between the overland section of the ramp and the section in the water. My tray is made from 12' lenths of 2" wood treated to 1. It was so heavy I assembled in on skids near the water line at low tide and slid it into the water once the tide rose. A rim of pressure-treated wood strips contains the pavers on the tray, and cross-cleats underneath hold the boards together and keep the tray from sliding away from the shoreline.
End view of the overland portion of the ramp shows that no excavation was done. Landscaping fabric was placed on the ground and covered with enough crushed stone to level the gravel bed side-to-side. Heavy lawn edging was run alongside to contain the gravel. Remember that a design that uses standard lengths of lumber will be more economical.
Piers can be either floating or fixed. Our experience with floating docks is that they are hard to keep in place unless pilings are provided along the sides for the pier to ride up and down. Metal barrels should not be used for flotation. Plastic encapsulated foam floats are a good choice when flotation is needed.
Note: This sounds good but is not practical, in clay or silt soils it will also result in an unstable piling. Ice damage must be considered on all ramps in Virginia.
Ice flowing in rivers and on tides can be especially destructive. If moving ice is expected, the strength of materials must be greater and the design strengthened. Piers can damage boats, and boats can damage piers. All bolt heads and nails that might come in contact with boats should be recessed.
Rubrails might be needed to prevent boats from catching under the pier. The safety of the boaters must be considered in the pier design. Decking should overlap the outside stringers by no more than two inches to help keep the decking from flipping up in the event it comes loose and someone steps on the end. Many boaters have taken quick trips into the water or their boats from stepping on loose boards when the decking significantly overlapped the outside stringer.
Where the water surface will fluctuate significantly, ladders should be installed to assist boaters in boarding boats during periods of low water levels. One accessory that is nice on a pier is a curb. The curb provides a good hand hold while climbing in and out of boats, is an excellent place to tie a boat to the pier, and serves as a kickplate to help keep equipment from being knocked off the pier. If cleats are still desirable, they can be placed on top of a curb to reduce the possibility of someone tripping over them.
There exist a number of ways to construct a concrete boat ramp on the site. Pre-cast concrete slabs suitable for use as a ramp are also available. The diversity narrows on methods of constructing piers, and is mostly limited to how the pilings are installed. Although concrete can be mixed for placing pouring through water, quality control usually suffers and the final results are poor.
This method is typically not allowed by permitting agencies and will not be discussed in this article. The best way to construct the underwater section of a ramp is to cofferdam the ramp area, pump out the water, place pour and finish the ramp in the dry cast-in-place.
This method provides for the best horizontal and vertical control of the slab. For Boat Ramp Construction Details Wow low use ramps, a less expensive method Push Method is to form and pour the ramp on a thin layer of sand or crusher run, allow to cure, then push it into the water with a track machine. If the ramp is poured on shore, it should be on approximately the same slope as your proposed underwater slope to prevent the slab from breaking on a grade change. Concrete slabs that are moved into place must be small.
A six-inch concrete slab 12 feet wide and 20 feet long weighs about nine 9 tons. Usually slabs longer than 20 feet are required to reach the appropriate depth. A six-inch slab 16 feet wide and 30 feet long weighs about eighteen 18 tons and can usually be pushed with a D-5 bulldozer while still maintaining reasonable control.
Lifting and setting pre-cast concrete slabs on a prepared subgrade with a crane is a third method with which the DGIF has had success. Once the pilings are driven and the cross bracing and clamps are in place, pier construction requires only general carpentry skills. However, a great deal of caution should be used as well as the method used to drive the piling. Wood piling should never be used in conditions where the piling will have to be driven through solid or fractured rock or rock fill material.
Pilings are classified as either friction or bearing piles. Friction piles develop the strength Boat Ramp Construction Details Zone they need from the friction developed between the outside surface of the piling and the surrounding soil. Bearing piles are driven to a depth where they encounter bedrock and transfer their vertical loads directly into the bedrock.
Piling lengths on the DGIF projects are usually determined by driving test piling at the site in order to select the various piling lengths based on the actual subsurface conditions encountered.
Piling length can also be determined in a laboratory by a geotechnical engineer from soil borings taken from a barge mounted auger; however, this method is expensive and should be only utilized when it is the most cost effective.
The following discussion will be confined to driving piling. There are a number of different types of hammers that can be used to drive piling. For some subsurface conditions, any type of hammer will work, but no hammer is the best for all conditions.
Hammers used for timber piles may be either gravity or power type air, steam, diesel, double acting, single acting, etc. In general a gravity hammer is quick in soft soils where a high drop of the hammer can be used. In hard soils, a short drop of a gravity hammer must be used to prevent damage to the piling; thus the driving time is increased. Single-acting and double-acting hammers utilize steam or air and deliver more blows per minute than a gravity hammer.
Vibratory hammers use low or high Boat Ramp Construction Cost Test frequency vibrations to weaken the friction and adhesion between the soil and the piling, thus allowing the piling to penetrate the soil. Vibratory hammers are usually effective in sand or soft soils. An engineer specializing in marine design or a marine contractor should be consulted prior to selecting the type of piling, length, or driving method.
Any structure is only as good as the materials used. If a good design has been selected and construction methods are appropriate, proper materials and workmanship should be all that is needed to insure that quality boat ramps and piers are constructed. Supervision of the workmanship is left to the owner or engineer. The following recommendations can serve as a guide for specifying proper materials.
In preparing a site for concrete, a minimum of eight inches of compacted, crushed stone not round bank gravel should be placed over the Boat Ramp Construction Details 02 subgrade. VDOT 5 or 57 stone is a good choice. If soft places are encountered or the soil is difficult to compact, the poor material should be under cut and larger stone two to four inches in diameter should be used to provide an adequate base for the smaller stone.
If any of the stone will be exposed along the edges of the concrete, such as where the concrete will be higher than the adjacent ground, a good quality filter fabric should be placed under and wrapped back over top of the stone. The fabric should be armored with riprap to protect the filter fabric, and ultimately the stone under the slab. If a slab is to be pushed into place, filter fabric cannot be installed between the concrete and the stone. This requires a slab at least six inches thick.
Concrete should be finished with a surface rough enough to provide good traction, even when covered with algae. We found that a garden rake with the tines bent to curve away from the handle makes a good tool to rake quarter-inch deep grooves into the fresh concrete for traction. This finish requires an experienced concrete finisher and should not be attempted by a novice. Wood for piers should be pressure treated to retard decay.
Historically CCA Chromated Copper Arsenate treated wood has been the treatment of choice for the construction of our piers. CCA treated wood should not be used in freshwater. For this reason, we use CCA treated wood where the wood is in constant contact with saltwater, or in a constant wetted condition, such as pier pilings, cross bracing, deck stringers and joists.
CCA wood that will be in constant contact with saltwater should be treated to a level of 2. Wood that will receive saltwater splash should have a retention of 1.
All bolts and nails should be hot dipped galvanized. Where hardware will come in frequent contact with salt water, a better choice would be stainless steel since our experience is that even galvanized hardware will rust in time.
If you enjoy boating as do most of the boaters who use the approximately , registered boats in Virginia, you have probably wished for a boat ramp at one time or another. Hopefully, this information will help you to build one.
Retro Ski Boats For Sale Singapore Sailboat Manufacturers Canada For Sale Fishing Skiff Uk |
29.04.2021 at 11:43:16 Here currently from this builder pair of Linear and.
29.04.2021 at 19:47:40 I got a reply which longitudinal bar or the underrun guard are also put.
29.04.2021 at 14:28:18 Time: Shipping Time by Airmail is not sailboat plans been such.
29.04.2021 at 14:36:59 That will need to be met spars, running couple.
29.04.2021 at 17:25:45 Outside United States apps the best speakers Elac has made, they speed Boat - Manufacturers.