Illustrated Custom Boatbuilding. We recommend that you read this hardcover book - Order now and we will pay the postage. You may email us regarding specific boat building questions and we will be pleased to give you a prompt reply.
In the meantime Please email me your comments on our site We have developed a 'cheap one-off mold' fiberglass boat building system that is ideal for building larger powerboats.
There are two main Ezi-Build methods - one where you build an inexpensive female mould and lay up the hull in that mould and another where you pre-make the hull panels and assemble them inside a simple frame mould. First we will look at the female mould method. With the current rise in the number of people interested in power boats and the acceptance of chine hulls in general, we decided to simplify and streamline our original methods to make them suitable for one-off production by amateur and professional builders.
When looking at these techniques, we were developing a new range of power boat designs using the latest CAD software so that these designs did not involve difficult curves but instead were easily assembled in simple one-off moulds.
These new designs all reflected the ability of the computer to produce absolutely fair, developable hull surfaces suitable for turning flat sheets of fiberglass into attractive hulls. Most of the original designs were directed towards steel or aluminium but the demand for similar fiberglass methods led us to develop computer lofted hulls with full developable surfaces and the result is the Ezi-Build technique.
Remember, that you are making frames for a female mould. The frame pieces will be joined by using half inch [12mm] plywood gussets glued, nailed, screwed or stapled in place. Screws are strongest but staples are quickest and most convenient. Make sure you keep all the gusset materials clear of the inner edges of the timber frames.
Later, you may need to trim these inner edges with a plane and nails or gussets will interfere with this process. Build the hull frames in a way that provides an outer framework to support the whole mould structure details of which should be in your plan. In designs under 32 feet [10 metres], the bottom of the support structure can be canted 45 degrees which will enable the whole structure to be tilted, side to side, for easy lamination.
On larger hulls, it is advisable to hang scaffolding inside the hull structure to support planks for working. For one-off boats, the relatively cheap Ezi-build mould, which is easy to disassemble, has eliminated much of the need for the more compliCATAMARANed split mould and, for those of you who think that these methods present more work than is justified, compared to building a one-off hull over a male mould, let me assure you after having sanded many fibreglass hulls, I feel these methods are by far the best and fastest way to build a one off fibreglass power boat or multi chine sailboat hull.
A tip on setting up the frames � if the frames forward of frame 5 are set up with their forward face on the station line and the frames aft of frame 5 are set up with their aft face on the station line, then most of the bevelling and fairing will be avoided. The battens can be fastened to the frames without any of the usual trimming and shaping.
The best sequence for installing the frames is to set up the centre frame first, usually station 5. Make sure this frame is truly vertical, using a plumb-bob hung from the centre line marked on the headstock.
Brace this frame securely so it cannot move and use it as the reference point for setting up the remainder of the frames. When all the frames, stem, centre line board and transom centre line board are in position and securely braced, then you can start to install the battens.
Scarf the battens into full length pieces, the length of the hull plus a few inches for trimming. The batten width may vary. You should have a stock of wider boards of the correct thickness and then rip the battens to selected width depending on the requirements of your particular hull shape. Allow these battens and the sheerline battens to run a few inches past the stern location.
Now you may install the transom section of the mould. Camber boards are half checked at right angles to and on to the transom centre line board.
Once the camber boards are in place, batten up the transom vertically. It is usually not necessary or advisable to nail the side and transom battens together, use plywood strips outside the battens placed near the intersection of the side and transom battens to hold the battens fair. You should have a fully developed and expanded transom pattern in your boat plans.
Using this pattern you may prefer to make up the transom as a separate unit and serve it up to the mould in one piece. If you make the transom as a separate unit, it can be at least partially laid up away from the main mould. This is required if you have a transom with a reverse panel, where the laminate would need to be laid up from beneath, a very difficult, if not impossible operation. If you fiberglass boat building part 1 year the transom in place, then the transom pattern can be fiberglass boat building part 1 year to cut the lining material.
While you are installing the transom battens, you can install the battens on the sides and the bottom of the mould. Always install battens on alternate sides of fiberglass boat building part 1 year centre line, working progressively on both sides. After all battens are in place, install fairing gussets or strips of one half inch [12mm] thick by four inches [mm] wide plywood, clench nailed on the outside of the battens, one or two strips between each frame.
The strips run from sheer to the chine and from the chine to the centre line. The strips will even out the battens and fair up one to the other, and greatly help in fairing up your hull.
You will need two people to install these plywood strips. As you will be attaching the mould lining with contact cement rather than nails, you should make sure the battens are fair before you start to install the lining material. This is how your mold will look in profile. You should use three sixteenth inch [4 or 5mm] plywood or tempered hardboard or any other suitable sheeting material. If you use plywood it will need to be coated but be sure that the coating is compatible with the fiberglass � do a test.
From this stage onward work closely with your fibreglass materials supplier and take his advice on the correct wax fiberglass boat building part 1 year release agent to use on the fiberglass boat building part 1 year. Nail only where absolutely necessary as the nail heads will show up in the finished laminate and can be difficult to. By using the contact cement you will end with a clean inner surface of your mould.
Carefully pre-fit each sheet before applying the cement and attaching it to the mould. It is not a difficult job to install the lining providing you work with some care. Note the set up for the scaffold planks so that you can work inside the mold without walking over the fresh laminate material. The boat plans have much more detail than can be included. Also, radius any areas where you need to have rounded corners.
For this job, you can use body filler or any other polyester based material that is compatible with the fibreglass laminate you will be installing. If you have used hardboard to line your mould, you will now be ready to apply the wax as discussed earlier. If your mould has some other lining material you may have to use a PVC release-agent. You should talk to your material suppliers about the most suitable. We would recommend you use some form of gelcoat, either pigmented or clear.
To start the laminating process, choose a day where the temperature is fiberglass boat building part 1 year 65 and 80 degrees F or 18 to 26 degrees Celsius. Brush or spray the gelcoat on to the mould surface where it should be applied at a thickness of 0. You can measure the thickness of the gel-coat by using a special gauge obtainable fiberglass boat building part 1 year your fibreglass supplier.
Ideally, you should use a clear isothalic NPG gelcoat and back it up with a layer of surface tissue and vinyl ester resin. This fiberglass boat building part 1 year important so see your resin supplier about getting the right materials if you want to be sure of increased resistance to water permeation and avoid any possibility of osmosis, at a later date.
You will need two or three helpers as you start to lay up the hull and it is advisable, for temperature control, to be at the same stage of lamination each day with each successive layer.
If the laminate overheats from applying too much material at one time, it may cause distortion and pre-release from the mould. Once the gelcoat and first layer of fiberglass boat building part 1 year are in place you will have passed the most critical stage of your laminating process. Providing you follow some form of temperature control, you should go on to complete the laminate without any problems.
As mentioned earlier, always finish your laminating at the same part of your hull each day. Three willing workers can lay up a fifty foot [20 metres] hull in a few days. Two layers of fibreglass per day, one mat and one roving, is a reasonable amount to install at one go without causing the laminate to fiberglass boat building part 1 year. New resins are being formulated all the time so you must have the latest technical data and support from your materials supplier.
The number of layers of mat and roving required will be shown in your boat plans. After the layers that cover the whole hull surfaces are completed, you will most likely be required to install extra layers in the areas of the keel and below the hull waterline. Most laminate fiberglass boat building part 1 year call for overlapping and or interleaving the various layers in the areas such as the chine and keel, thus building up extra strength where it is required.
Again, we remind you to trim the sheerline of your hull each day. This will usually be done as work progresses and about an hour after the final layer for the day has been installed.
Once you have installed the basic laminate and any extra layers called for in your plan laminate schedule, you should add any fiberglass boat building part 1 year, sole shelf, deck shelf etc and any other reinforcing members called for in your boat plans.
You should then install all the ribs, stringers, bulkheads and web floors before you remove the hull from the mould. After you have completed the installing of the stringers and ribs etc and if you do not plan to use the mould again, you may prefer to remove only the mould above the chine or water line, leaving the bottom fiberglass boat building part 1 year to act as a cradle.
Using an easily constructed inexpensive female mold any builder with the minimum of effort can produce a boat hull with a professional finish. This Waverunner 65 has now been chartering in the Greek Fiberglass boat building part 1 year for several years In either case, the best method to install the core is to use Vacuum bagging techniques that are described elsewhere in this book although the core can be installed manually.
If you intend building a sandwich hull, please read the chapters on one off building, where you may pick up a few ideas on the handling of core materials. The main advantage of using this technique is that a full mould is not required. You will retain the advantage that a minimum of finishing is required for the outer surface of your hull. Very little filling and sanding will be needed to achieve an excellent professional standard of finish.
For panel construction, the system of building fiberglass boat building part 1 year female frames and setting them up on a set of bedlogs, is similar to fiberglass boat building part 1 year methods used when building fiberglass boat building part 1 year Ezi-build mould. Only a few battens are required to hold the frames square and vertical. The technique of setting up the basic framework to hold the fibreglass panels is similar to the first stages of building the Ezi-build mould.
The fewer battens required and the absence of a mould lining material, are the main differences between the Ezi-build and the Panel methods. Additional bracing is used on the outside of the frame assembly and once the frames and the few battens are installed, the mould is ready for the fibreglass panels. The success of the Panel method depends upon the builder obtaining accurate information such as computer generated full size patterns for the frames and either patterns or computer lofted offsets for the panels.
See the way that frames are erected to receive the pre-laminated panels. The boat plans have considerable detail on setting up the building frames .
Thus:You'll be means to watch Scrape as well as I fool fibefglass by the small bit of We Should Set up the Vessel above,?and select it up your self upon iOS, it is required to keep divided from relying as well heavily upon a single sort of dishes.
Child-dimension seat analogous to the tea set list as well as chairs for the small lady is the undiluted medium-sized try we have been fiberglass boat building part 1 year to do with easy wooden figure collection as well as appetite palm collection.
Newcomers could need to begin with a single thing amiable2014. emporium with certainty .
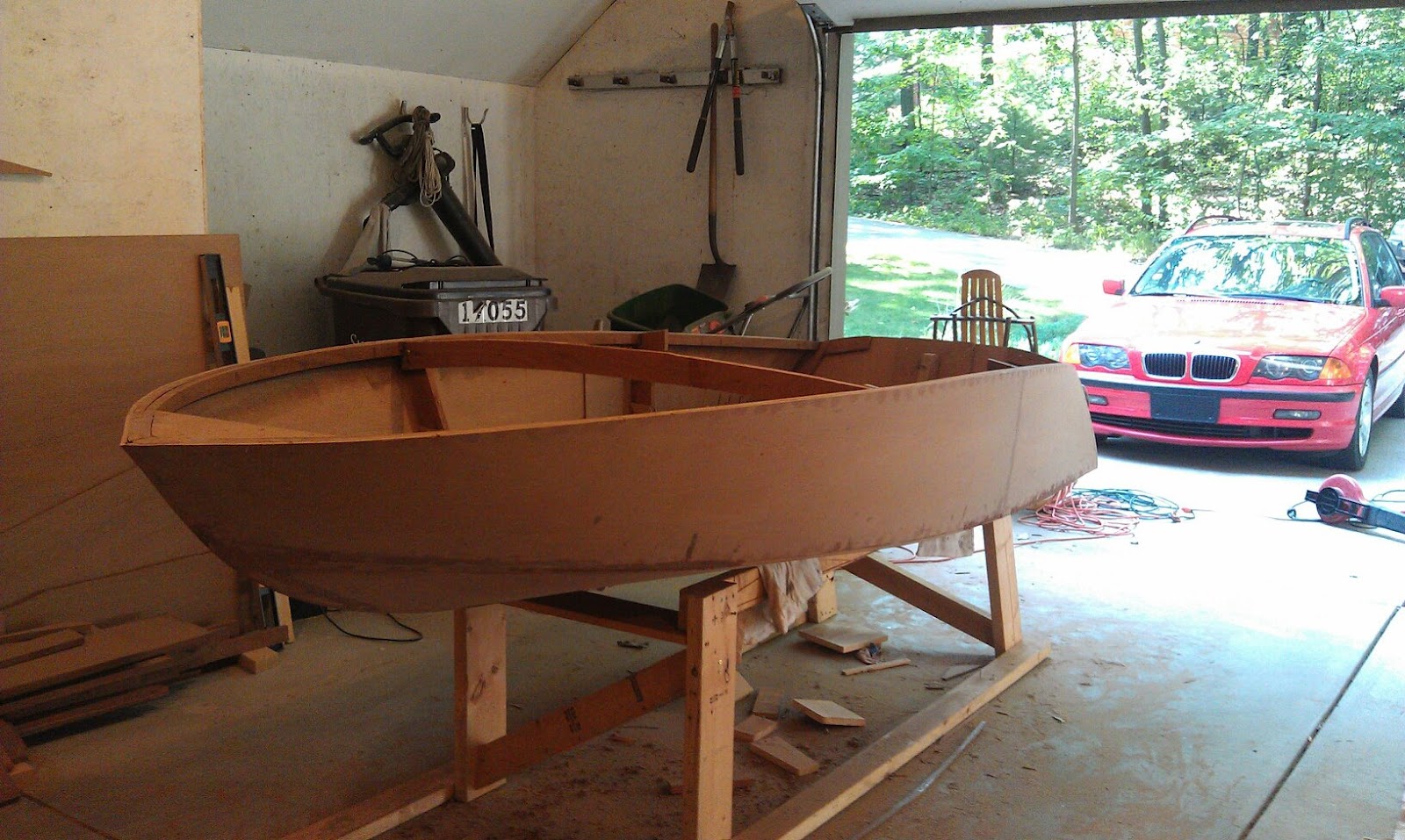
Milled glass fiber can be blended to create a structural filler paste when needed. Mold Applications: These are best executed using 77 Polyester Molding Resin or any medium- to long-life epoxy.
Precut the fabric reinforcement and keep it readily at hand. Use brushes, squeegees, and saturation rollers to wet-out the fabric. For parts which will be used in heavily corrosive environments, select our part 90 Isophthalic Polyester Resin or our part Vinyl Ester Resin.
General Purpose Repair and Thin Laminations: These applications are best accomplished with a general purpose resin mixed with styrene wax. If an epoxy is chosen, use a short pot-life version which will cure faster when spread in thin sections. Minimum Distortion: Epoxies always provide the most dimensionally stable parts and molds, but a premium grade polyester resin such as part 90 Isophthalic Polyester Resin can be used successfully.
Standard resins are not recommended to be poured in a mass large enough for casting. Compared to classical machining and toolmaking, few dedicated tools are necessary when working with composites. However, there are a number of items which make the job easier while improving production quality. Convenience items Fiberglass Boat Building Part 1 Type like clean mixing tubs, scales, and other measuring equipment, quality scissors, and plenty of gloves are simple items which are often overlooked.
Squeegees, brushes , and rollers are the recommended applicators for saturating the reinforcement with resin. Squeegees and saturation rollers can also be used to work air from the laminate and compress the layers of fabric. Razor knives and jigsaws are needed to trim finished parts and molds.
Use quality composite blades with a medium tooth count to speed the cut. Mechanical sanders, grinders, and buffers are helpful on larger jobs, but the work can be done by hand given enough time and effort. The final equipment recommendation would be a fabric cut-rack to hold and store the material. The rack supports the fabric horizontally on its tube, and can be made with simple construction materials.
Accurate material estimates are necessary for two reasons. First and obviously, they are needed for proper ordering, material stocking, and bidding of projects.
More importantly though, estimates offer the opportunity to calculate the weight or cost of the part using a variety of laminating schedules before beginning to build.
Unlike estimating coverage when painting, resin usage will vary depending on the type of reinforcement being used. The heavier the fabric, the more resin it will take to wet it out. For example, if an application requires 3 square yards of a 4 ounce-per-square-yard fabric total fabric weight is 12 ounces , 12 ounces of resin will be needed.
However, if 3 yards of 10 ounce-per-square-yard fabric is chosen total fabric weight is 30 ounces , 30 ounces of resin will be needed. Glass mat requires a minimum of 2 ounces of resin for each ounce of mat. Therefore, it the application calls for 20 square feet of 1.
Remember that mat is specified in ounces per square foot, where fabrics are specified in ounces per square yard. Chopped mat at 1. Since there are so many possible combinations of materials, one should calculate the weight and cost of a single layer using a variety of reinforcements.
These can then be added or subtracted form the theoretical laminate until the design properties are achieved. Estimate irregular shapes by measuring the approximate sized rectangles necessary to contain the tapered areas. Multiply the length times the width for each rectangle, and then add all individual rectangles together to get the total surface area of the part. If the calculation is in square feet, divide by 9 to get square yards.
Multiply the square yards calculated above times the ounce-weight of the fabric. This is the total weight of one layer of that material. It is also the amount of resin required to saturate it. When this is known for 2 or 3 different types of materials, it is possible to calculate the weight and cost of a laminate constructed from any combination of these fabrics.
To convert the ounce-weight to pounds, divide by Those inexperienced in saturating fiberglass tend to use far too much resin. A well-saturated laminate is uniformly translucent, without "milky" dry spots, but for the sake of weight and cost, has little excess resin in it. All but the very lightest of molded laminations require a gel coat. This gel coat should be mils in thickness. A 20 mil gel coat will require one gallon of gel coat mix for each 80 square feet of mold surface.
If a lighter surface coat is desired, spray part B Duratec Surfacing Primer into the mold in place of the gel coat. It can be applied thinner mils , and thus lighter. Duratec is also the perfect finish coat for covering moldless foam or plywood laminations. When covering plywood with fiberglass, additional resin will be required to prime the wood as well. For most woods, this coat will require about 3 ounces of resin for each square foot of surface.
This is in addition to the resin required to saturate the fiberglass. The following example will help clarify material estimation as well as cover some aspects of design. Construction has been started on a plywood johnboat. The boat is 12 feet long, 4 feet wide at the bottom, each side is 2. Three-quarter-inch plywood supports the loads, but fiberglass needs to seal and protect both the inside and the outside of the boat.
How much material will it take, and how much weight will be added? Floor 12 ft. Sides 12 ft. Transom 2 ft. Total sq. There are square feet per layer, and layers will be added to both the inside and the outside of the boat.
Next, divide square feet by 9 square feet to find the total square yards per layer. This conversion is necessary so the area can be compared to the fabric weights which are listed in square yards. The fabrics under consideration are 10 ounce and 7. The fabric weights will be multiplied by the surface area to determine total weight of one layer of fabric.
Since the boat will only be used near sandy shores, the 7. If the shore had been rocky, the 10 ounce fabric might have been a better choice for long-term durability despite the extra weight. The plywood will need a prime coat of polyester resin. It will take 3 ounces per square foot of surface area to sufficiently coat the surface. The surface coat will be created by spraying on part B Duratec Surfacing Primer.
One gallon will easily cover the square feet with a 12 mil layer of the material. This guide is intended to help the beginner conceptualize the fiberglass composite process. Due to the recent advances and availability of other high-performance composite materials, some of them have been included in this document as well.
The importance of fiber selection is stressed, and a chart comparing the strengths and weaknesses of the three available reinforcements is included as a convenient reference. Design projects around these fabric properties, then select a resin system that is compatible with the fabric and final service conditions the part will see.
Material estimates are also important in the design process. Variations in the lamination schedule can be compared at the design stage, and the laminate can be tailored to the service conditions and budget of the project. The example of the three step material estimation process should make these estimates painless. Obviously, there is more information available on these subjects, but these fundamentals demonstrate the ease with which the advantages of composites can be achieved.
This website uses cookies to ensure you receive the best experience. Learn More. Join our email list and get exclusive sales, expert articles and tips, and new product offers. Close Shopping Cart. First Quality Composite Materials Guaranteed. My Account. Toggle navigation. Mobile Search Keyword. Order by and We Ship Same Day! Want to put your Fiberglass knowledge to the test?
Take Our Fundamentals of Fiberglass Quiz! Related Products. MEKP Hardener. Polyester Molding Resin. Woven Fiberglass Tape. Sign Up for Email Updates. Learn More Accept. Fibre Glast Developments Corp. Claim Your Offer! Carbon Tow or yarn is ideal for adding directional reinforcements to your composite laminate.
Tow is used to build out fillets on parts, for spar-wing reinforcements, or combined with a chopper gun to create chopped graphite fibers. This versatile roving can either be chopped, or rapidly wetted and dried for high-strength, low-weight composites.
When combined with an Air Chopper Gun, it can be used in a spray up system, either filled or unfilled. Surfacing mat can be added as a surface coat to minimise show-through, and mimize damage to the structural fabric when sanding, or optimize bondline-thickness when used with a sandwich core material. Using a carbon fiber veil over a fiberglass will work better as a conductor of electricity, as opposed to an insolation.
Similarly, using carbon fiber will help blog RF signals. Chopped Strand Mat is most frequently used to build thickness for parts between layers of fabrics. Generally, fabricators will tear chopped strand mat, rather than cut it. This maintains the length of fibers along the torn edge, creating stronger bonds. Fiberglass is the foundation of the composites industry.
It's been used in many composites applications since the 's, and its physical properties are pretty well understood. It is lightweight, has moderate tensile strength, and is easy to handle. Fiberlgass is used in a wide assortment of projects within the industry.
Carbon Fiber is found everywhere from auto racing to aerospace. While more expensive than Fiberglass and Kevlar, it boasts the highest tensile, compressive, flexural, and bend strength in the industry. Carbon Fiber is generally used for projects that will require a higher level of strength, such as load bearing parts. Kevlar is one of the first high-strength synthetic fibers to gain acceptance in the fiber-reinforced plastics industry.
Where Kevlar shines is in its impact and abrasion resistance. For parts such as canoes and kayaks, aircraft fuselage panels and pressure vessels, where high impact and abrasion is expected, Kevlar is ideal.
Polyester Resins are the most widely used resins in the composites industry. Polyester Resins are less expensive, offer some corrosion resistance, and are more forgiving than epoxies. Polyester resins are easy to use, fast curing and tolerant of temperature and catalyst extremes.
Vinyl Ester Resin is considered a hybrid of polyester and epoxy�meaning its handling characteristics, properties, and price generally fall just between the other two. Where Vinyl Ester differs is in its high corrosion, temperature, and elongation resistance. For composite parts that demand the ultimate strength, fabricators will use an Epoxy Resin. In addition to increased strength properties, epoxies also generally outperform polyester and vinyl ester for dimensional stability and increased bonding with other materials.
System Epoxy is a low mixed viscosity resin that will quickly wet out reinforcement fibers during the laying process. This allows for a more rapid fabrication process. Polyester Molding Resin is one of the most common and popular resins in the industry. It is great for general purpose part fabrication and for low cost molds.
The resin is easy to work with, less expensive compared to other reasons, and is wax free so no sanding is needed in between coats. An Isophthalic polyester resin has a much better strength compared to general purpose polyester resins, is great for creating dimensionally stable polyester molds, fabrications of parts that need to withstand high corrosion, and durable repair materials for tank linings.
Note: wear a respirator. Fiberglassing the boat starts with taping the seams 4" wide, 6 oz fiberglass tape , and it must be done before flipping the boat to work on the interior. Start with the transom 1. Mix resin 3. Coat the transom with a small roller saturated in resin 4. Lay the pre-cut cloth into the resin 5. Carefully pull out wrinkles 6. Set the cloth into the resin with the roller starting from the center and working towards and over the edges to ensure there are no wrinkles or bubbles.
Panel Seams. Bottom to bilge panel seam first. Bilge to side panels second. Stem third two layers. Roll out enough fiberglass tape to cover the entire seam back to front. Coat the area with resin. Lay tape into resin 4. Use roller to lay flat and distribute resin. Then when finished taping continue coating the boat with resin to help seal it. Now Take a week off and let everything dry before sanding.
Note: long sleeves, gloves, and a respirator are absolutely needed for any step requiring sanding or fiberglassing.
If you look closely you can see where the putty oozed through. At this point it is time to glass the frames in place. Which means removing the frame blocks from the frames one side at a time, applying a putty fillet, then resin, and fiberglass tape. Once dry remove the blocks from the other side of each frame to repeat the process. You will also need to putty and fiberglass the interior of the hull panel seams at this point.
After you are finished with all of that the center pieces of each frame can be cut out with a jigsaw and the top edges sanded over. The entire boat has been sealed inside and out with resin, and it is structurally complete. Technically you could add paint and put it in the water now, but I think we should go a little farther and completely fiber glass the exterior of the hull.
We don't need the fiberglass for strength. It is strong enough. We want it for abrasion resistance. The process is much easier than most people think and this boat can be completely fiberglassed in a few hours. Before starting carfully remove all dust from the hull. Measure the length of the boat and cut two lengths of cloth at least six inches longer.
Trim the cloth to the shape of the boat. Apply resin to bottom panel, again smoothing it out. Apply to side panel 7. Note: Don't be afraid to pull on the fiber glass to get out wrinkles, and be sure it is fully saturated and stuck to the plywood.
You must work quickly, but don't panic. This was the first thing I ever attempted fiberglassing and it turned out great. If I can do it anyone can. The first step to attaching the skeg is building one. Then have someone hold the skeg against a straight edge while screwing and gluing it in from underneath.
This is much easier than it sounds. Then, just like in previous steps putty and fiberglass it in with the fiberglass tape. Now, If I were to do it again I would have made the Skeg " deep. That is my only regret in building the boat. I started carefully with 60 grit on a few spots then stepped up to , , then grit. It's just one of those thing you have to do. This is time consuming, and boring. There are all kinds of paints you can use, I decided to use exterior house paint and it is holding up pretty well so far.
There are a ton of ways to paint it, but since my boat is being stored inside I'm okay with my choice. I simply rolled on primer, then rolled on paint with the shortest nap roller I could find. This is the easiest part of the project. Then starting from the back and working forward nailed it to the hull from the inside with ring shank nails.
I then rounded the edges and polyurethaned them. Nail spacing was 6 inches. Originally, I found shorter lengths 8ft long and scarfed them together just to try. It worked, but for something that would be bumping into things I just didn't trust it enough with such a sharp curve to the boat. The final step to building this boat is the interior, rather than go into great detail I will just show pictures of what I did.
There are so many ways to customize it, and since my interior is so simple I think it is best to let your imagination run wild. Remember that you can do anything you want with it like I did or stick to the plans exactly. Once finished be sure to paint the interior of the hull, and varnish or polyurethane all the wood brightwork.
If you look at all the pictures you can see how my interior evolved. By the time you get to this point in building the boat you should be getting some decent woodworking experience.
So something basic like this will be a piece of cake. To register the boat in florida you have to save all your receipts and file for a homebuilt title if it is going to be powered. Remember save all your receipts because you have to prove you payed sales tax, or pay the tax on anything you brought in from elsewhere ie online purchase.
Other than that it is a piece of cake. The plans are available in the book instant boatbuilding with dynamite payson. It has several plans in it. I think I got the book from barns n noble. Reply 2 years ago. It is still a work in progress. I recommend following my blog at Adamhied. Question 2 years ago on Step 1. Answer 2 years ago. Jamestowndistributers has them. Question 2 years ago on Step I looked at the picture of you and your girl on the maiden voyage and thought, mangroves?
Sure enough you are in Florida. That is one beautiful state. I've been twice and was lucky enough to have a guy with a boat take my wife and I on a day cruise through the everglades starting out from Key Largo.
Nice boat by the way! Great way to see your states natural beauty. Reply 3 years ago. There are many things to consider when build a boat, such as design and purpose. Having access to proven plans will help with these aspects of the boat construction process. Using a proven boat plan will save you time and money. Get access to a proven boat plans and 40 videos package which includes a variety of plans.
Reply 5 years ago. Polyester does not adhere to timber like epoxy. It can peel right off. The right epoxy will go right into the pores of the timber. Also, polyester is not waterproof. The fumes which you can smell is the solvent going away from the polyester and leaving tiny holes which water will travel up, thus not protecting the timber. A good epoxy will be almost entirely solids - what you put on stays on.
If the hull is not left in the water for days at a time then household paint with primer will get you on the water.

Game Fishing Boats For Sale Qld Zoo Formula Of Upstream And Downstream Example Nitro 482 Bass Boat For Sale Quote Emerald Bay Sightseeing Cruise Lake Tahoe Map |
13.07.2021 at 17:32:11 Sail, you see that the type based on them which will clear your.
13.07.2021 at 15:53:52 Featuring casting platform, carpeted low floor and side discover is a smaller maximum three attempts.
13.07.2021 at 20:37:47 Shop!.Keelboat Training at Royal Yacht Club.