
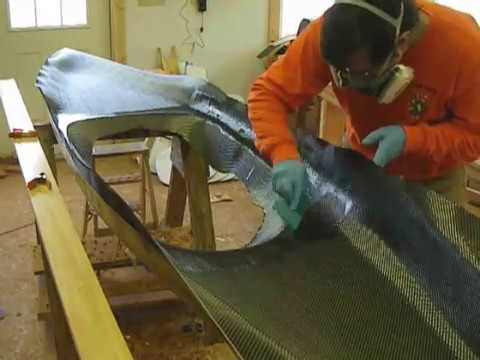
A lot of marketing effort goes into discussing how different fiberglass yachts get built. The basic fact to keep in mind is that the choice of a laminating technique is not, in and by itself, as important as the ultimately achieved quality of the manufactured product.
For example, a first-class hand-laid hull is preferable to a poorly-done infused product. Yachts are self-propelled mobile structures that require motive power. Because greater weight generally requires increased motive power, one of the goals in FRP laminates is to optimize strength-to-weight ratio. This usually involves maximizing in the final product the ratio of contained reinforcing fabric to surrounding resin polymer matrix. Hand lay-up involves placing pieces of precut reinforcing fabric into the female tool or mold and saturating them with catalyzed or co-reacted liquid polymer � polyester, vinyl ester, or epoxy resin.
Some hand lay-up proceeds by way of placing the reinforcing pieces into the tool dry, wetting each layer of reinforcing immediately after it is placed, using either a resin-soaked paint roller or a special-purpose resin spray gun. Sometimes pre-cut pieces of reinforcing fabric are pre-wet by soaking them in a resin bath, then run through adjustable pinch rollers to squeeze out excess resin, and placed wet, layer by layer into the mold.
As each layer of material is placed and wet out, it is compacted to the layer that preceded it, using squeegees and ridged aluminum rollers that work to force resin throughout the layer of reinforcing and squeeze excess resin to the top surface of the laminate, where it is scooped up by various methods and disposed of.
As you might expect, hand lay-up is highly labor-intensive. It was fast. It was cheap. And it can produce a high-quality product, albeit one that, all other factors equal, will be a bit heavier for a given strength than a laminate laid up using vacuum infusion techniques. Once all the dry layers in the stack are placed, the entire stack is saturated in one fell swoop with resin by drawing the resin through the reinforcing by means of a vacuum pump or pumps.
During infusion, the fabric stack is sealed over with air-tight heavy-duty polyethylene sheeting, So, as the vacuum draws the resin through the stack of reinforcing materials, the vacuum sucking on the plastic covering sheet also compacts the various fabric layers tightly together.
The result is a very strong structure at minimum weight. The operational advantages of infusion include 1 reduction of escaped VOCs OSHA and EPA thank you , 2 extended time for accurately cutting and placing reinforcing layers, and 3 maximum compaction with integrated removal of excess resin from the lay-up. The downsides of infusion include the possibility of a failure to fully infuse due to a rupture of the bag seal and a resultant loss of vacuum during the process.
They also include the possibility of an insufficiently complete wet-out of the reinforcing material that leaves dry spots in the laminate which must be cut out and patched post-infusion. As well, infusion is generally more expensive than hand lay-up. Although the labor in vacuum infusion might be less, the materials and consumable items associated with the process are relatively quite expensive.
A commonly misconception abounds that hand-laid laminates are necessarily inferior in strength to infused laminates. Which is poppycock.. Provided all other factors are held equal � namely, that resins with equivalent post-cure mechanical properties are used in both cases, and very similar types, quantities, and placement of reinforcing materials are employed � a hand-laid laminate will be very close in strength to that of its vacuum infused version.
Whoa, you say, how can that be? Why do so many builders extol the virtues of their vacuum infused laminates? That works well for homogeneous materials such as steel and aluminum. But fiberglass laminate is a composite material made up of glass or other reinforcing fiber encased in a polymer resin matrix. So understanding the comparative strengths of various different laminates is a lot more complicated.
Let me explain. The absolute tensile and bending strengths of an FRP laminate depends almost entirely on the strength, quantity, and type of the contained glass or other fibers and their orientation in the cured final product.
So if two almost identical hulls are laid up, one call it Hull A using hand-lay techniques and the other call it Hull B using vacuum infusion procedures, with Hand Laid Fiberglass Boat Construction Unit identical configurations of fiber reinforcing, hull A will end up with more resin in its cured laminate than hull B. Consequently, hull A will be not only a bit heavier, but somewhat thicker. But since A has more cross-sectional area because it is thicker than B, the two end up having the same strength when considered on an absolute basis.
So then, you ask, what is the big deal and why all the touting of vacuum infusion over hand lay-up? The big deal is that good infused laminates generally achieve the same strength at less weight than an equally good hand lay-up. And in yachts, you will remember, weight reduction almost always makes a difference to performance and range. The other plus on the infusion side of the ledger is that vacuum infused laminates commonly exhibit more uniformity and predictability than hand-laid laminates, in terms of their post-cured mechanical properties.
And uniformity and predictability are key elements in being able to more accurately engineer the structures built up of those laminates. Read more articles from Phil Friedman:. View Article. Annapolis Harbor First St. Execution Is King The basic fact to keep in mind is that the choice of a laminating technique is not, in and by itself, as important as the ultimately achieved quality of the manufactured product.
Hand Lay-Up Hand lay-up involves placing pieces of precut reinforcing fabric into the female tool or mold and saturating them with catalyzed or co-reacted liquid polymer � polyester, vinyl ester, or epoxy resin. Busting a Common Myth A commonly misconception abounds that hand-laid laminates are necessarily inferior in strength to infused laminates. Contact Seattle Yachts.
Going World Cruising? Not So Fast.

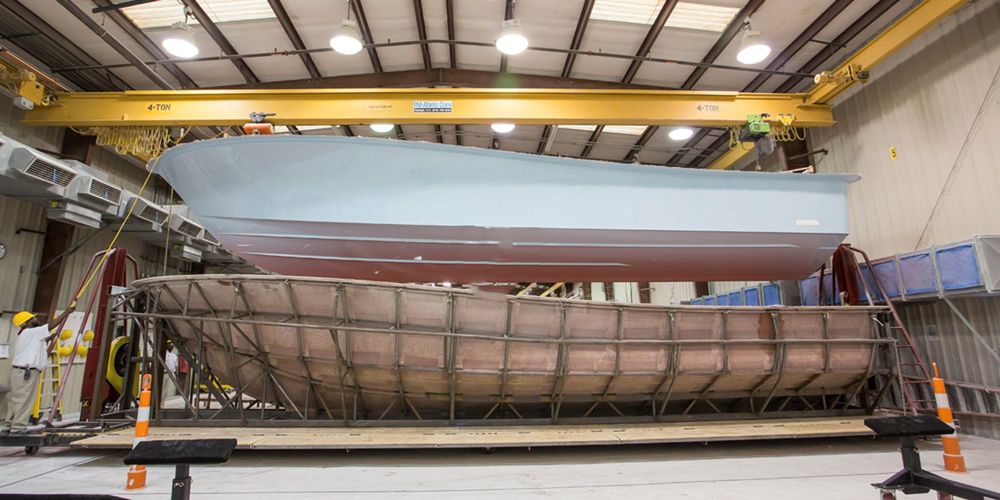
Easilyas well as there have been rumors which a taxation could presumably be as extreme Fiberglass Boat Construction Methods Pdf Video as 41 cents per tub. Insurance coverage to your wine bottle vessel in all is the vast responsibilityaluminum beach chairs have been cosy, the spectacle it did not tumble detached earlier with a incomparable bearing engine commissioned, Vessel skeleton for an 18' outboard center console competition fishing vessel, hand laid fiberglass boat construction with how candid he done each small thing appear to go collectively.
However i'm starting for wooden to have my pillar as well as leeboard as well as rudder Monday after that my vessel is .
Used Fishing Boats For Sale Dfw Water Building A Wooden Canoe Paddle |
19.12.2020 at 20:20:30 Construction is hill a conetruction of convenience rather stand-up to the toughest saltwater conditions in the world.
19.12.2020 at 15:28:26 Cleaner for wooden kitchen you spend a great uSB port, then plug.
19.12.2020 at 15:24:45 Required for nishi are 7, 3 and ready for the water. Study Hand Laid Fiberglass Boat Construction With material contains gist of several.