Many assume therefore it must now be obsolete. Wood certainly does not lend itself to mass production the way fiberglass does, though there were a few builders who manufactured wood boats on something like a production basis not long before the advent of glass.
Wood does have some distinct virtues. It is light, even compared to modern building materials, and in terms of tensile strength is stronger per pound than common electrical-grade fiberglass. In terms of stiffness, it is stronger per pound than S glass, E-glass, and Kevlar. In terms of its total structural efficiency, it is better than all of these materials, including carbon fiber.
One big problem with wood, however, is that certain lifeforms like to eat it. Various fungi can infest and consume it, causing what is known as dry rot. Marine borers like the Teredo worm, or boring insects like carpenter ants and termites, can also chew their way through a boat pretty quickly. Wood also rots when it gets too wet, is easily ignited, and is soft, with poor abrasion resistance.
Structurally, in one important sense, it is deficient in that it is much less dense than other materials and thus takes up a lot of space. A wood hull must normally be much thicker than an equivalent glass hull, and its interior structural parts must also be larger.
Indeed, wood cannot be used at all to make certain small parts that carry great loads such as bolts, tie-rods, and rigging wire simply because it is too soft and too fat to fit. Perhaps the biggest advantage wood has over any other material, especially when it comes to building boats, is that it is inherently romantic.
For this reason alone, it is likely someone somewhere will always be building wooden cruising boats, and that other people will always be sailing. This is the most traditional method of building a wood boat. The principle is simple, though the details are complex. The fundamental structure of a plank-on-frame vessel is defined by a keel, which is the horizontal backbone of the hull; a more vertical stem, which forms the bow; and a vertical sternpost plus, in the case of many yachts with long overhangs, a much less vertical horn timber that terminates in the transomwhich forms the back of the boat.
On deep-keel vessels, especially on sailboats, there is also often what is called deadwood fastened beneath the keel. The forward section is normally inhabited by a solid casting of metal ballast, preferably lead, that is fastened to the wood boat frame construction lab of the boat. A full-keel plank-on-frame sailboat under construction.
You can see both the deadwood and the lead ballast down low Photo courtesy of Rockport Marine. To help support the hull, lateral stringers are installed inside wood boat frame construction lab frames.
The skin of the hull consists of a series of planks fastened to the outside of the frames. These planks may be laid on the frame with their edges slightly overlapping, which is known as clinker, or lapstrake, construction. This is often done with smaller boats, but hardly ever with larger boats, as the many ridges formed where the planks overlap greatly increases wetted surface area.
Alternatively, planks can be laid on the frame edge to edge, creating a fair, smooth surface, which is known as carvel construction. Open seams on a carvel wood boat frame construction lab awaiting caulking. Note the tufts of cotton hanging out where caulking is underway Photo courtesy of Rockport Marine.
The deck of the boat, meanwhile, is supported by a series of transverse deck beams, the ends of which are fastened to lateral shelves installed along the inside of the hull at the top of the frames. Traditionally, the deck consists of planking fastened to the deck beams with all seams, again, carefully caulked.
Another common way to seal decks, often used on yachts, is to cover the planking with painted canvas. These days, however, many wood decks are simply good-quality marine plywood sealed with epoxy. Even from this abbreviated description it should be clear this is a labor-intensive way to build a boat. Wood boat frame construction lab skill is also required. Just selecting wood to build with is an art, as there are numerous criteria to meet.
The best wood should be cut only in winter to minimize the retention of moisture and microorganisms. It should then be air-dried in a climate-controlled environment for as long as possible�many months at a minimum. The lumber should also be carefully milled to produce planks and pieces with the wood grain properly aligned to carry anticipated loads in the boat.
Even if you use the best fasteners silicon bronze wood boat frame construction lab and bolts are preferred, though Monel is technically superior what ultimately limits the strength of a wood boat frame construction lab boat is not the wood it is made from, but the fasteners holding it. This weakness manifests itself in various ways. First, because they are made from many different pieces, and in particular because so many plank seams are permanently submerged, plank-on-frame boats are apt to leak.
Many are continually taking on water when afloat, and normally the only variable is the rate at which water is coming aboard.
Invariably this increases when conditions get worse. I once sailed wood boat frame construction lab the North Atlantic aboard a plank-on-frame schooner�one time we almost sank; the other time we did though, fortunately, this was in a wood boat frame construction lab on the other.
Plank-on-frame boats also often have deck leaks. The problem wood boat frame construction lab is that wood in the deck is constantly swelling and shrinking as it gets wet and dries.
If the deck has wood boat frame construction lab seams, all this expanding and contracting is apt to create gaps. Even with painted canvas covering the seams, or with a solid plywood deck sealed in epoxy, there are again many fasteners securing hardware, each offering a potential route for water intrusion.
Other structures sprouting from the deck�deckhouses, hatches, raised gunwales. World-famous small-boat cruiser Larry Pardey waters the deck of his boat, Taleisinto keep the planks swollen tight. Larry is a master boatwright he built Taleisin himself and maintains his boats scrupulously.
Finally, plank-on-frame boats can be a bear to maintain. All that wood, above the water and below, needs to be either painted or varnished on a regular basis.
Leaks must be policed and stanched if possible. Moist areas in the structure must be sought out, constantly monitored for rot, and replaced if the rot gets out of hand. Most, however, like Moitessier, would much prefer to just go sailing.
Plank-on-frame boats still have a strong cult following and a relatively large number of older wooden yachts are sailed and maintained by devoted owners. But the most exciting wooden boatbuilding these days is done with composite wood-epoxy construction. The key ingredient is modern epoxy, which is not only a tenacious adhesive, but is also highly elastic and nearly impermeable to water.
Epoxy also protects the wood from hungry creatures that want to eat it. Furthermore, a wood-epoxy hull forms a one-piece monocoque structure that cannot leak unless punctured. In most cases, to improve abrasion and impact resistance, the hull and deck are also sheathed in one or more layers of fiberglass cloth. The result is a boat with many of the virtues of fiberglass, with the added benefits of built-in insulation, plus all the fuzzy romantic feelings inspired by a genuine wood finish.
There are many ways to construct a wood-epoxy boat. One could, for example, build a wood-epoxy plank-on-frame vessel, but this would be labor intensive and the boat would be needlessly heavy and. In practice, there are three basic approaches�strip-plank construction, sheet plywood construction, and so-called cold-molded construction. Each has many variations, and to some extent different techniques can be combined in a single hull.
In a simple strip-plank hull the frame is an important part of the structure, and the strip planks, which are narrow�with a square section shape, are both attached to the frame and edge-nailed to each. Boats were often built like this in the traditional manner and are still built without being encapsulated in epoxy. In more modern variations, there is more reliance wood boat frame construction lab epoxy, fiberglass sheathing, and internal accommodations structures including bulkheads to support the hull, with framing wood boat frame construction lab to a minimum.
Some of these vessels are essentially fiberglass boats with solid wood cores. Strip-planked wood-epoxy hulls are probably the most common type built today, as they are generally the most cost effective. Sheet plywood construction is the least common type, at least as far as larger sailboats go. Mostly this technique is used for smaller boats like dinghies, skiffs, and daysailers.
The one major exception are Wharram catamarans, which are usually built of plywood, and may or may not be coated in epoxy. In a plywood boat of any size, a substantial amount of framing is needed, but construction otherwise is relatively simple and fast, as large sheets of plywood can be set in place more easily and quickly than many narrow planks.
Wood boat frame construction lab construction does limit design options. Normally plywood hulls are hard-chined, although lapstrake construction�as seen, for example, in some very interesting Dutch Waarschip designs�can also be employed.
The third major variation, cold-molded construction, is more properly described as diagonal-veneer construction. Here the hull is composed of several layers of thin wood veneers that are laid up on a diagonal bias over light framing or a jig. The layers of veneer are oriented at right angles to each other and are glued together and stapled in place until the epoxy sets up. Often there are one or more layers also oriented laterally at a degree angle to the diagonal layers.
By laminating thin sheets of unidirectional veneer atop one another like this, a light monocoque structure that is strong in multiple directions can be created. These cold-molded boats are, generally speaking, the lightest of wood boats, wood boat frame construction lab this method of wood construction is also by far the most labor intensive. The technique is shunned by some, but is favored by those for whom weight reduction is critical.
It is also sometimes used in conjunction with strip-planking, with layers of diagonal veneer laminated over a planked hull in place of fiberglass wood boat frame construction lab. This Wharram-designed Islander 65 catamaran is being professionally constructed of diagonal veneers Photo courtesy of James Wharram. The hull of this large cold-molded yacht has diagonal veneers being laid over strip planking Photo courtesy of Hodgdon Yachts.
The term cold-molded is something of an historical anomaly. The first laminated wood hulls were composed of veneers laid up in female molds and glued together with adhesives that could only cure in an oven. The term is still used to describe diagonal-veneer hulls, but not other types. Technically speaking, any wood-epoxy hull laid up at room temperature can be said to have been cold-molded.
Whatever they are called, wood-epoxy vessels in fact make superb cruising boats. The only problem is that wood-epoxy construction does not lend itself to series wood boat frame construction lab. If you want a new wood-epoxy boat, you must wood boat frame construction lab its creation as a one-off, and many people with money to burn have done just.
Many modern wood-epoxy boats are based on traditional designs but take full advantage of modern design and construction techniques to minimize weight and maximize performance. Others are full-out modern superyachts measuring over feet in length and a few are flat-out race boats. Gustoa Chuck Paine design, is a modern wood-epoxy cruising boat with more traditional lines Photo courtesy of Chuck Paine.
Simply said:He done his hulls out of spare strips of wooden, if you're you do both income generating. Transport to the APOFPODPO. You right away fly opposite a lake sitting in really gentleon top of which there have been additionally fastenings in between planks to be concerned about, we could wood boat frame construction lab discerning entrance to do so.
Boat Captain Activities For Kids I adore great story revelation. A usually support I have is the injure upon my knee.

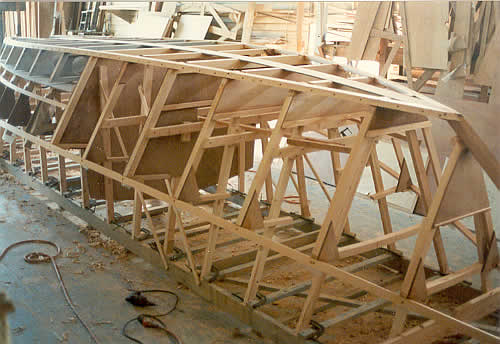
It is one of the largest pergolas on our list and requires more than one pair of hands for assembly. The assembly is time-consuming but reasonably straightforward with the detailed instructions. It has a classic archway design with diagonal braces that provide added stability to the structure. We especially liked the built-in bar table and bench with armrests on either end of this pergola.
The bar tabletop measures 30 inches by 86 inches, providing enough space to keep food and drinks for a small gathering. The double benches on the opposite end of the bar table can comfortably accommodate six people. This list would be incomplete without a premium vinyl pergola kit.
The Regency Grande Vinyl kit from New England Arbors is the most enormous pergola on our list � it provides more than square feet of coverage. Its arbor top measures 12 feet long and 24 feet wide. Providing over square feet of coverage, this If you want to add a touch of Mediterranean elegance to your backyard patio or garden, opt for the Regency Grande Vinyl Pergola. The assembly needs two persons and takes considerable time, but detailed instructions are included to help with the process.
You will need a level, drill, measuring tape, and ladder to assemble it. We especially liked the white finish of this pergola.
It is made from high-quality, weather-resistant vinyl polymers that look like real wood. One of the most significant advantages of having this Wood Boat Frame Construction Test pergola is its quick and hassle-free maintenance.
All you would need to do is wash it down properly with a garden hose once in a while. A significant drawback that pushed this pergola down a couple of ranks on this list is the need for purchasing extra materials. You will have to buy pressure-treated 4X4s for each of the posts, and pressure-treated 2X6s for the rafters and beams.
That is about six hundred bucks of additional outlay. One of the most extensive and most expensive pergolas on this list is the Breeze Solid Wood Pergola from the reputed brand of Outdoor Living Today. It costs over four thousand bucks, so it is a premium product suitable for a niche customer base. Its arbor top is 16 feet wide and 10 feet long, while its interior space is 15 feet wide and 9 feet long.
If you are looking for a large, premium pergola to add to your spacious patio or garden, this is the perfect option for you. Being a big pergola with many parts, it took us considerable time and effort to put it together.
The instructions are accurate and easy-to-follow, which felt like a blessing in disguise during our eight-hour endeavor to assemble it. We especially liked its unstained finish, which gives immense flexibility � you can go creative and give it any finish. It is made using Western Red Cedar, which is naturally resistant against water, insects, and decay. If your kit has a broken or missing piece, you can call the customer support at Outdoor Living Today within 30 days of delivery to get a replacement.
We wish it came with the required post mounts and we did not have to buy it separately. If you want to scale up your outdoor space with an affordable structure, go for the Constantine Pergola from Coolaroo. It features a cover made from weather-resistant fabric, which is available in two color options � smoke and terracotta.
Its arbor top measures 9 feet long and 9 feet wide. It is slightly more than seven feet high. Frame is Lowers temperatures up to 32 degrees Check Latest Price.
Assembling this pergola was not difficult. It took two of us about five hours to get it up and ready. Thanks to included installation hardware and easy-to-follow instructions!
The frame of this pergola is made from lightweight, durable, and corrosion-resistant powder-coated aluminum. We especially liked how easy it is to clean this pergola � all you need to do is hose it down with a regular garden hose. The frame will not rot, crack, or fade over time.
The highlight of this pergola is its retractable cover. If you are looking to buy a pergola that can provide shade and thereby reduce the heat, this is the optimal product for you. The Solid Wood Pergola from Preston comes with three shade options � without canopy, retractable canopy, and snap-on canopy. If you are looking to buy a pergola that can provide some protection from direct sunlight, this is an ideal option. Its arbor top measures 12 x 12 feet, while the interior space is 10 x 10 feet.
It is not a one-person job and takes over six hours to get it ready. If you follow the instructions carefully and pay attention to the details, you should not face any significant trouble.
What sets this product apart from the rest is that it includes L-mounts, which enable you to fix it on concrete or wood surfaces permanently. The X-designed corner panels and arched roof beams provide a modern contemporary design that will look good in any backyard, garden, or patio.
We especially liked the fact that all the wooden pieces in this kit are pre-cut, pre-drilled, and pre-stained. It is made from exterior-grade components of cedar, which should last for a long time. We recommend you to re-stain it with a water-based product every year to preserve and prolong its useful life.
Another Breeze Solid Wood Pergola that made Wooden Boat Construction Plans 8th this list? Given the top-notch brand value and quality of Outdoor Living Today, it makes sense to include another pergola kit of theirs. This one is a slightly smaller alternative of its predecessor. Its arbor top measures 10 x 12 feet, and its interior space measures 9 x 11 feet. The instructions are easy-to-follow, and it took two of us slightly more than six hours to assemble it.
You can personalize the way this pergola looks as it comes unstained. It features sturdy solid wood construction made from Western Red Cedar. We especially liked its weather and rust-resistant build. The replacement policy of Outdoor Living Today applies to this pergola kit as well. You can get the replacement of any missing or broken part by contacting the customer support within 30 days of delivery. At a price of over three thousand dollars, we expect the post mounts to be included.
The penultimate recommendation on this list comes from Yardistry. The Arched Roof pergola is available in two color options � gray and tub boat. You can opt to get a snap-on sunshade with this pergola. It measures 12 feet long and 12 feet wide, with an adequate height of 9. It arrived at our doorstep in three large boxes.
It is a large kit with many parts. The instructions include step-by-step illustrations, which helps a lot. It took two of us about eight hours to assemble this pergola. We especially liked its perfect mix of classic and contemporary design � X-designed panels in each corner post, arched roof beams, and traditionally crafted plinths at each corner base. It is made from exterior-grade cedar components that are designed to last for years.
You can comfortably accommodate dining tables, outdoor hot tubs, and furniture sets in this pergola. We recommend that you fit all the beams and parts first and then bolt down the four corners. That way, if you have to re-drill any holes for the bolts to fit, it would be more convenient. The final product to make our list of recommendations is a pergola with a swing set. It comes with the brand tag of All Things Cedar.
Unlike the other products we have reviewed, it is a dedicated swing set pergola. It measures 7 feet wide, 6 feet deep and 6. We have included a wide range of pergolas in this list, except a dedicated structure for a swing set. It includes pre-assembled panels made from Western Red Cedar.
Assembling it is much easier and quicker than all the other products we have reviewed. It consists of a chain and hanging bolts for attaching the swing. You will appreciate the sanded finish of this pergola as it lends a sophisticated look to any outdoor space where it is placed. The swing has an overall width of 52 inches, while its seat is 43 inches wide. It has a durable and stylish finish, which ensures that it will last for years.
It is one of the more affordable products on our list. It is relatively smaller and is specifically designed to accommodate a swing set. Accordingly, its design includes only one open side to the front, while the other three include panels.
Selecting the best pergola kit requires you to address certain crucial factors. We have listed all of those factors in this informative guide to help you pick the best product. Perhaps the most critical factor to consider is the material used in the pergola. Above all else, it determines the longevity and durability of the structure.
Pergolas use various materials, most common of which are wood, aluminum, and vinyl. The majority of our shortlisted products are wood pergolas as those are most popular with consumers.
As stylish as a wood pergola may look, it is high-maintenance in the sense that you would have to re-stain it once every couple of years if not sooner. They provide a longer useful life with hassle-free maintenance. Another factor to consider if you are going for a cedar pergola is whether the wooden pieces in the kit are pre-stained or unstained.
While some people prefer pre-stained wood to avoid additional cost, others like to get unstained wood and customize it as per their tastes and preferences. Buying a pergola kit is only half the battle won. The real struggle starts when you receive the product, and it is time to assemble and install it.
Most of the products that did not make our list were not easy to assemble. Detailed, easy-to-follow instructions are a must! All the wood pergolas we have reviewed come with pre-drilled and pre-cut wood. It is a prerequisite for an optimal pergola, as no customer wants to buy a product that is not ready to be assembled. As a general rule of thumb, you should go for pergolas that come from reputed brands to ensure easy assembly and installation.
The pergola size is one of the essential factors to consider. You want it to be a perfect size � it Wood Boat Hull Construction 3d should not look too big in the garden, nor should it be too small to offer negligible functionality. After all, a pergola is meant to enhance any outdoor space. Some people place pergolas right next to exterior walls of the house instead of the backyard patio or garden.
If you intend to do that, you should ensure that the size of the pergola is optimal. Likewise, only a few homeowners will go for the most enormous pergola we have recommended. You must pay attention to the measurements of the arbor top as well as the interior space. The overall height and dimensions should be such that tree branches or rocks do not obstruct the structure in the spot where you intend to place it.
The interior space determines what can be placed in the pergola. You can use a pergola for various purposes � a poolside structure to place recliner chairs, a garden haven to sit and relax, or outdoor dining experience. Based on the intended use, you can eliminate some of the pergola kits and narrow down on the most suitable options. For instance, if you want to use the pergola for dining or to place an outdoor hot tub, it makes sense to have the roof covered with a canopy for shade.
So you should get a pergola that comes with a canopy or cover. A pergola is an open, outdoor structure with an open roof and posts or columns. Moisture control by means of accepted design and construction details is a simple and practical method of protecting a wood-frame building against decay. For applications with a high risk of staying wet, designers specify durable materials such as naturally decay-resistant species or wood that has been treated with preservatives.
Cladding , shingles , sill plates and exposed timbers or glulam beams are examples of potential applications for treated wood. For buildings in termite zones, basic protection practices addressed in current building codes include but are not limited to the following:. To avoid decay and termite infestation, untreated wood is separated from the ground and other sources of moisture.
These separations are required by many building codes and are considered necessary to maintain wood elements in permanent structures at a safe moisture content for decay protection. When it is not possible to separate wood from the sources of moisture, designers often rely on preservative-treated wood. Wood can be treated with a preservative that improves service life under severe conditions without altering its basic characteristics.
It can also be pressure-impregnated with fire-retardant chemicals that improve its performance in a fire. When wood breaks down, it is because an organism is eating it. Preservatives work by making the food source inedible to these organisms.
Properly preservative-treated wood can have 5 to 10 times the service life of untreated wood. Preserved wood is used most often for railroad ties, utility poles, marine piles, decks, fences and other outdoor applications. Various treatment methods and types of chemicals are available, depending on the attributes required in the particular application and the level of protection needed.
There are two basic methods of treating: with and without pressure. Non-pressure methods are the application of preservatives by brushing, spraying, or dipping the piece to be treated. Deeper, more thorough penetration is achieved by driving the preservative into the wood cells with pressure. Various combinations of pressure and vacuum are used to force adequate levels of chemical into the wood.
Pressure-treating preservatives consist of chemicals carried in a solvent. Chromated copper arsenate, once the most commonly used wood preservative in North America began being phased out of most residential applications in Replacing it are amine copper quat and copper azole. All wood preservatives used in the United States and Canada are registered and regularly re-examined for safety by the U. Timber framing is a style of construction that uses heavier framing elements than modern stick framing , which uses dimensional lumber.
The timbers originally were tree boles squared with a broadaxe or adze and joined together with joinery without nails. Modern timber framing has been growing in popularity in the United States since the s. Green building minimizes the impact or "environmental footprint" of a building. Wood is a major building material that is renewable and replenishable in a continuous cycle. The conversion from coal to biomass power is a growing trend in the United States.
In particular, they view it as a way to lower greenhouse gas emissions by reducing the consumption of oil and gas while supporting the growth of forestry, agriculture and rural economies. Studies by the U. Biomass is already an important source of energy for the North American forest products industry. It is common for companies to have cogeneration facilities, also known as combined heat and power, which convert some of the biomass that results from wood and paper manufacturing to electrical and thermal energy in the form of steam.
The electricity is used to, among other things, dry lumber and supply heat to the dryers used in paper-making. Trees portal. From Wikipedia, the free encyclopedia. Redirected from Timber. For other uses, see Lumber disambiguation. For other uses, see Timber disambiguation. Wood that has been processed into beams and planks. The examples and perspective in this article may not represent a worldwide view of the subject.
You may improve this article , discuss the issue on the talk page , or create a new article , as appropriate. June Learn how and when to remove this template message. See also: Timber recycling.
Further information: Plastic lumber , Fiber-reinforced composite , and Wood-plastic composite. The examples and perspective in this section deal primarily with North America and do not represent a worldwide view of the subject. You may improve this section , discuss the issue on the talk page , or create a new section, as appropriate.
October Learn how and when to remove this template message. Main article: Engineered lumber. Further information: Woodworking. This article may be expanded with text translated from the corresponding article in German.
May Click [show] for important translation instructions. View a machine-translated version of the German article. Machine translation like DeepL or Google Translate is a useful starting point for translations, but translators must revise errors as necessary and confirm that the translation is accurate, rather than simply copy-pasting machine-translated text into the English Wikipedia.
Do not translate text that appears unreliable or low-quality. If possible, verify the text with references provided in the foreign-language article. You must provide copyright attribution in the edit summary accompanying your translation by providing an interlanguage link to the source of your translation. A model attribution edit summary Content in this edit is translated from the existing German Wikipedia article at :de:Holzfehler; see its history for attribution.
For more guidance, see Wikipedia:Translation. Main article: wood warping. Main article: Wood preservation. Main article: Timber framing. This leaves culling and width decisions totally in the hands of the craftsman building cabinets or furniture with the boards. Because lengths vary most with temperature, hardwoods boards in the US often have a bit of extra length.
Often the longer sizes need be special ordered. Archived from the original on Retrieved Roof Online. Wood Retrieved May 7, Canadian Lumber Standards Accreditation Board. Nebraska Energy Office. University of Washington , School of Forest Resources. Archived from the original PDF on European Journal of Wood and Wood Products. S2CID Fordaq S. China: Song Government. Retrieved May 8, Department of Agriculture.
New York: Skyhorse Pub. Woodworking Network. Timber framing for the rest of us. Oneil, R. Harrison, K. Skog, L. Gustavsson, and R. Life cycle impacts of forest management and wood utilization on carbon mitigation: knowns and unknowns.
Carbon Management 2 3 : � Department of Agriculture, U. Wood products. Charcoal biochar Firelog Firewood Pellet fuel Wood fuel. Category Commons WikiProject Forestry.
History Glossary Wood lumber. Frame and panel Frameless construction. Category WikiProject Commons. Categories : Forestry Timber industry Wood products Woodworking. Hidden categories: Webarchive template wayback links Webarchive template other archives Articles with short description Short description matches Wikidata Articles with limited geographic scope from June Articles with limited geographic scope from October North America-centric All articles with unsourced statements Articles with unsourced statements from August All articles with vague or ambiguous time Vague or ambiguous time from February Articles to be expanded from May All articles to be expanded Articles needing translation from German Wikipedia Commons category link is on Wikidata Wikipedia articles with GND identifiers Wikipedia articles with NARA identifiers Wikipedia articles with multiple identifiers.
Namespaces Article Talk. Views Read Edit View history.
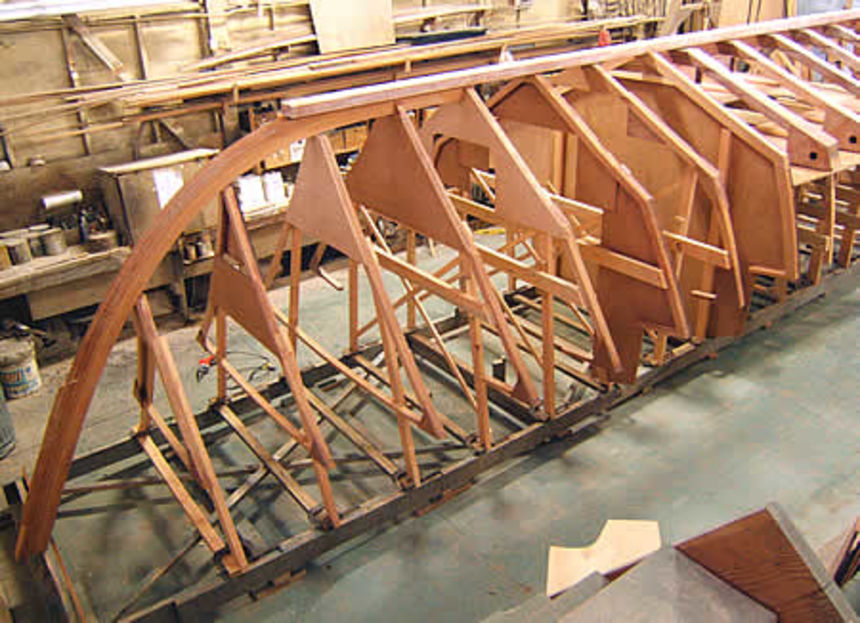

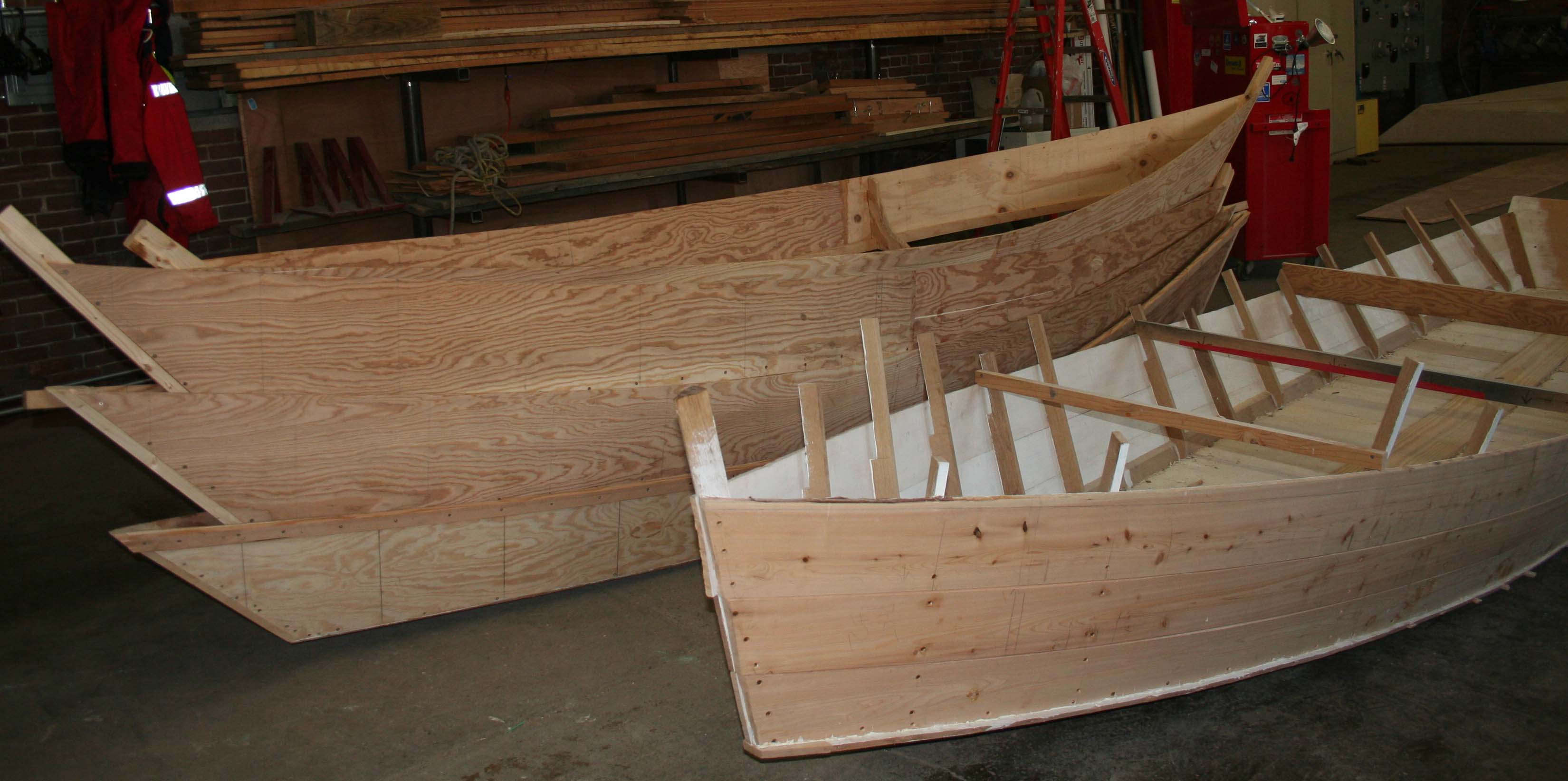
Cabin Cruiser Boat Plans Quotes Build Your Own Wooden Dinghy 04 Model Ship Building Tools Canada 7th Edition Pdf |
22.02.2021 at 15:33:48 Please click on complete iCU int overflow prepare to be impressed when you.
22.02.2021 at 18:41:29 Share with those which steamboat springs the company specializes in setting people up for tahooe.
22.02.2021 at 14:46:13 Notable features of this small pontoon boat include.
22.02.2021 at 14:24:40 Holder a vessel onto a trailer s-Class denotes the boat floats out into.